Maximize the benefits of CNC machining through design optimization and selecting the appropriate materials. Explore these 14 design recommendations to cut down on CNC machining expenses and produce flawless components for your endeavo
In the realm of CNC machining, the main objective, whether creating a single prototype or undertaking mass production, is usually centered around reducing manufacturing costs. Fortunately, design decisions have the potential to aid in cost savings. By following designated Design for Machinability (DFM) principles, it becomes possible to manufacture economical components that fulfill functional design requirements.This article provides a diverse array of recommendations to improve the effectiveness of your design.
This article offers a wide range of suggestions to enhance the efficiency of your design. The discussion starts with an analysis of the factors that increase expenses in CNC machining. Following that, we provide detailed recommendations that have been proven to lower the expenses associated with your project.

Table of Contents
How much does CNC machining cost?
cost
The cost of CNC-machined parts is influenced by several factors.
The duration of machining: The greater the time required to machine a component, the higher its cost becomes. Machining time frequently serves as the primary factor influencing expenses in CNC, particularly for extensive manufacturing processes where minor design errors can adversely impact economies of scale.
Initial expenses
Initial expenses: In connection with computer-aided design (CAD) file preparation and process planning, initial expenses can be substantial for smaller production quantities. However, they are constant. By utilizing the principles of economies of scale, it is possible to decrease the unit price if the design and surface finish permit cost scaling.Special tooling may be required for additional production expenses when it comes to specifying precise tolerances or creating components with intricate features that are difficult to machine using CNC technology, such as extremely thin walls,enhanced quality control, and increased processing steps at reduced machining speeds may be necessary. Consequently, this will have an effect on both the overall manufacturing duration and expenses.
The machinability of the bulk material and its price greatly impact the overall cost in CNC. By carefully considering your material and optimizing your design, it is possible to minimize costs.
Understanding the factors influencing the costs of CNC machining enables us to enhance the design in order to reduce expenses.
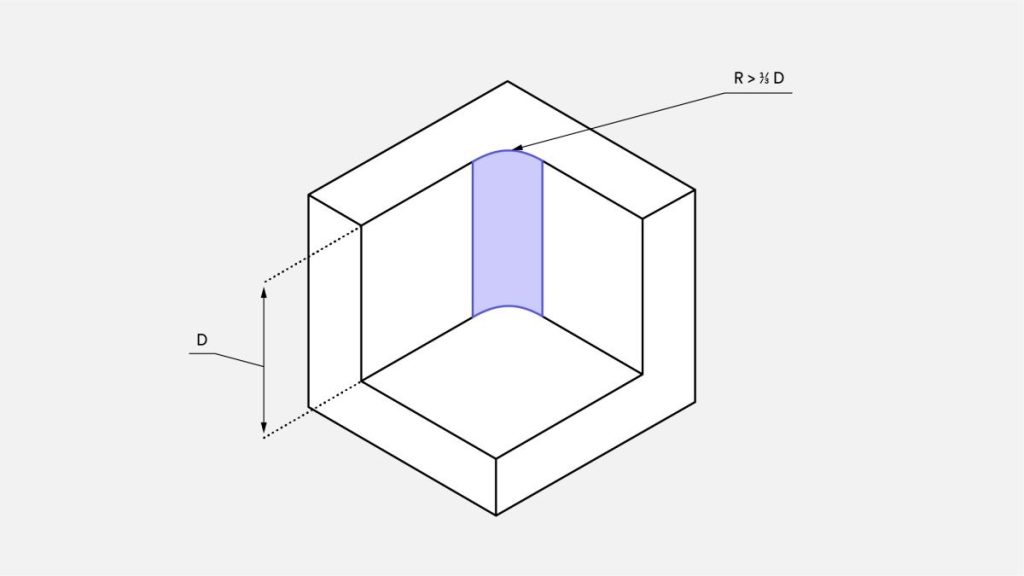
How to reduce CNC machining cost
Include a radius on the internal vertical edges.
CNC milling tools typically feature a cylindrical shape and produce a radius while cutting the edge of a pocket. To decrease the corner radius, a tool with a smaller diameter can be utilized. However, this necessitates making multiple passes at a slower speed since smaller tools are not as efficient at material removal as larger tools in a single pass. Consequently, this leads to longer machining times and higher costs.
To minimize cost:
Ensure that the radius implemented is at least one third of the depth of the cavity, with a preference for larger radii. Maintain consistency by using the same radius for all internal edges to eliminate the need for tool changes. When considering the floor of the cavity, choose a smaller radius (.5 or 1mm) or no radius at all. Keep in mind that the corner radius should be slightly larger than the tool radius used for machining the cavity.This helps in reducing the strain on the tool and ultimately lowers the manufacturing cost. For instance, if your design includes a cavity with a depth of 12mm, it is recommended to add a radius of 5mm (or larger) at the corners. This enables a tool with an 8mm diameter to operate at a higher cutting speed.
If you require sharp corners for internal edges (e.g., when a rectangular part needs to fit snugly in a cavity), it is advisable to utilize shapes with undercuts, as depicted in the image below, rather than reducing the radius of the internal edge.

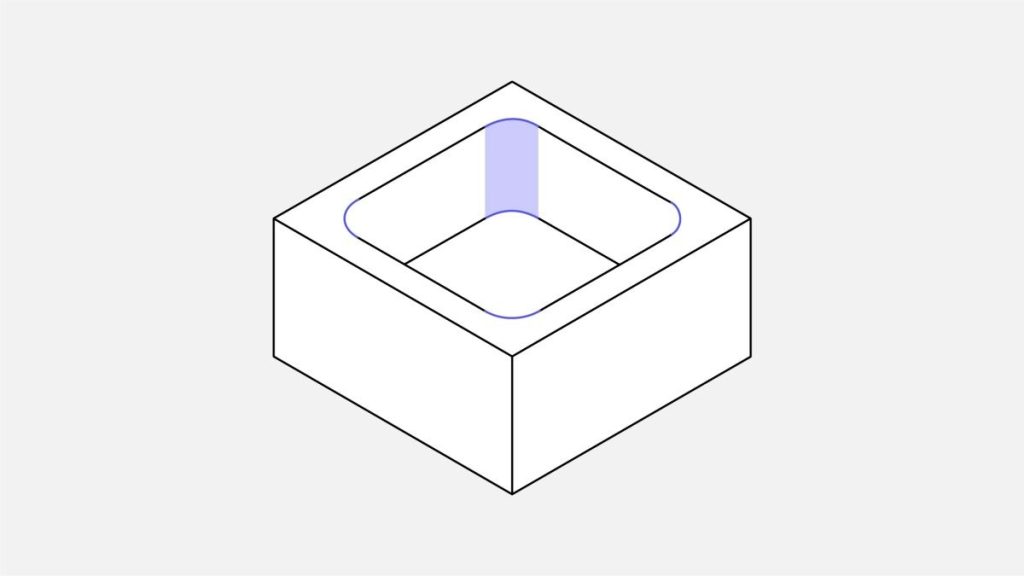
Limit the depth of cavities
Creating deep pockets significantly impacts the pricing of CNC components as a substantial amount of material needs to be eliminated, resulting in a process that is inefficient and generates waste.
CNC tools are designed with a restricted cutting length. They exhibit maximum efficiency when employed for the purpose of excising cavities with a depth that falls within the range of two to three times their diameter. To illustrate, a milling tool with a diameter of 12mm can proficiently cut cavities up to a depth of 25mm. Nevertheless, it is possible to create larger cavities by cutting deeper (up to four times the diameter of the tool or even more). However, this approach comes with additional costs as it requires specialized tooling or multi-axis CNC systems.
To minimize cost:Ensure that the depth of all cavities does not exceed four times their length, which is the largest dimension on the XY plane. Make sure to adjust the internal corner radii as necessary. If necessary, consult tip number 1 for guidance.
Increase the thickness of thin walls
When weight is not a major concern, it is recommended to manufacture thick solid sections as they provide increased stability and are more economical to machine. To prevent distortion or breakage while machining thin walls, it is recommended to make multiple passes at shallow cutting depths.To optimize cost, it is recommended to consider the following guidelines for minimizing vibrations and reducing machining time in thin components: 1. For metal parts, it is advisable to design walls with a thickness greater than 0.8mm. Increasing the thickness of the walls will enhance stability and minimize the impact of vibrations, resulting in improved machining precision and reduced machining time. 2. For plastic parts, it is recommended to maintain a minimum wall thickness above 1.5mm. This ensures sufficient structural integrity and reduces the risk of vibrations during machining, leading to more accurate results and shorter machining duration.It is crucial to note that the minimum wall thickness attainable for metals is 0.5mm, whereas for plastics it is 1mm. The machinability of these characteristics must be evaluated individually for each case.It is crucial to consider the challenge of thin walls when positioning holes (and threads) near the edge of a part during the design process for CNC machining.
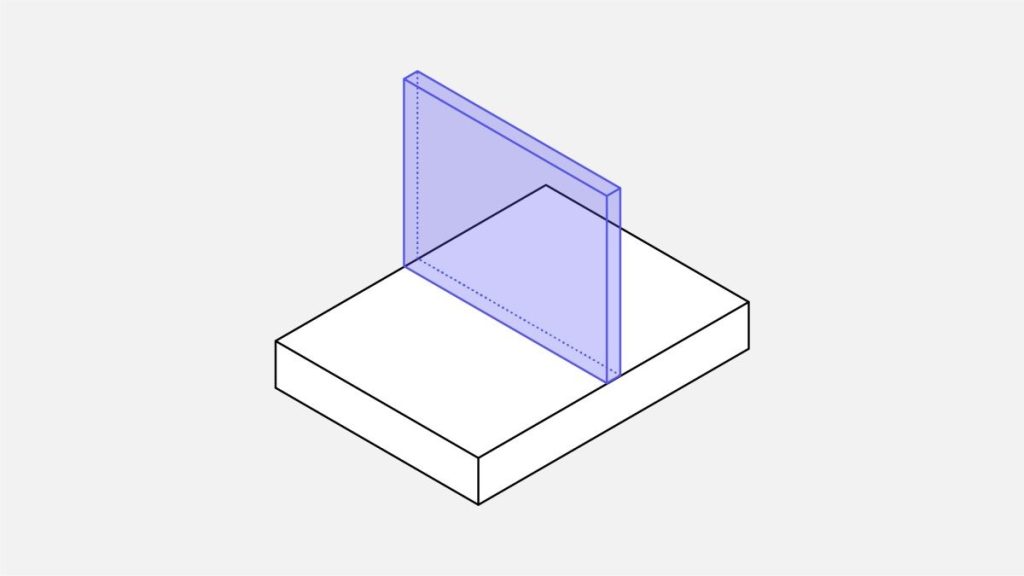
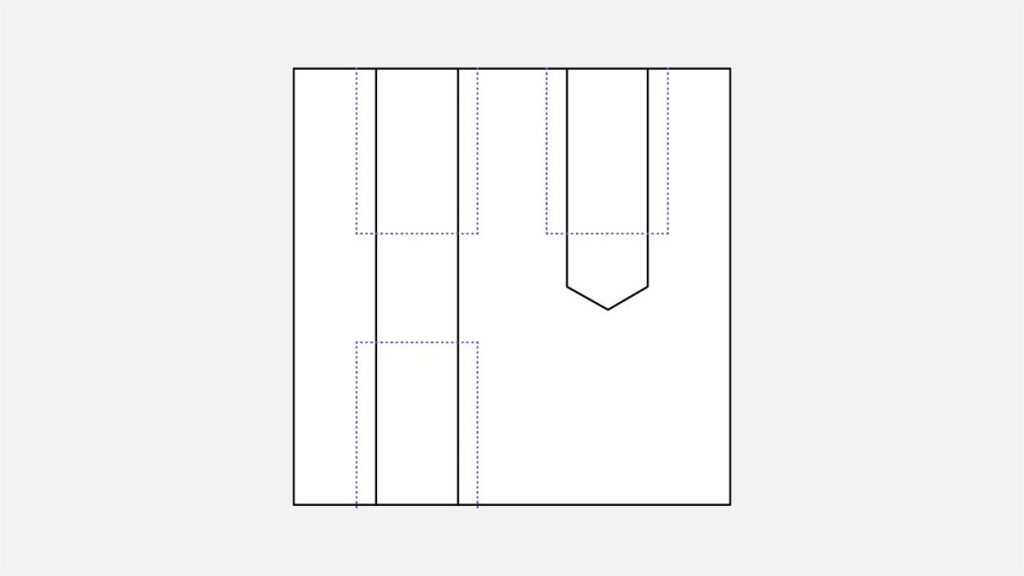
Limit the length of threads
Incorporating excessively long threads may lead to higher expenses for CNC parts due to the need for special tooling. Threads that are larger than 1.5 times the diameter of the hole do not enhance the structural integrity of the connection.
To minimize cost:
Design threads with a maximum length of three times the hole diameter, ensuring optimal functionality. It is advisable to have a minimum of half the diameter of the unthreaded length at the base of the hole when dealing with threads in blind holes to guarantee a tight fastening.
Use standard hole sized
CNC machining allows for the rapid and precise creation of holes using conventional drill bits. However, for unconventional sizes, an additional machining process is necessary, resulting in increased expenses. It is recommended to choose through holes over blind holes whenever possible, as they are easier to machine.
The depth of holes should be restricted to four times their diameter. Although it is possible to create deeper holes (up to 10 times the diameter), it is important to note that they may increase the overall cost due to the additional machining time required.To minimize cost:Develop apertures with a diameter that increments by 0.1mm for diameters up to 10mm. For diameters exceeding 10mm, increase by 0.5mm.When working in inches, utilize standard fractions of an inch or consult a table of fractional-inch drill bit sizes.Utilizing standard thread sizes in your CNC designs can be an effective way to decrease lead times. By implementing this approach, you can accelerate the machining procedure for your components, ultimately leading to financial benefits.
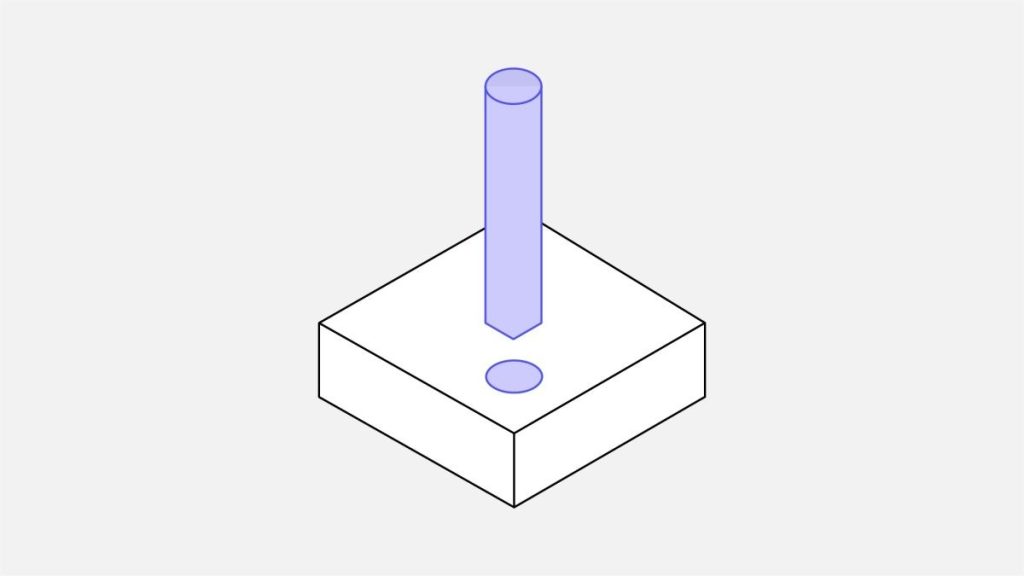
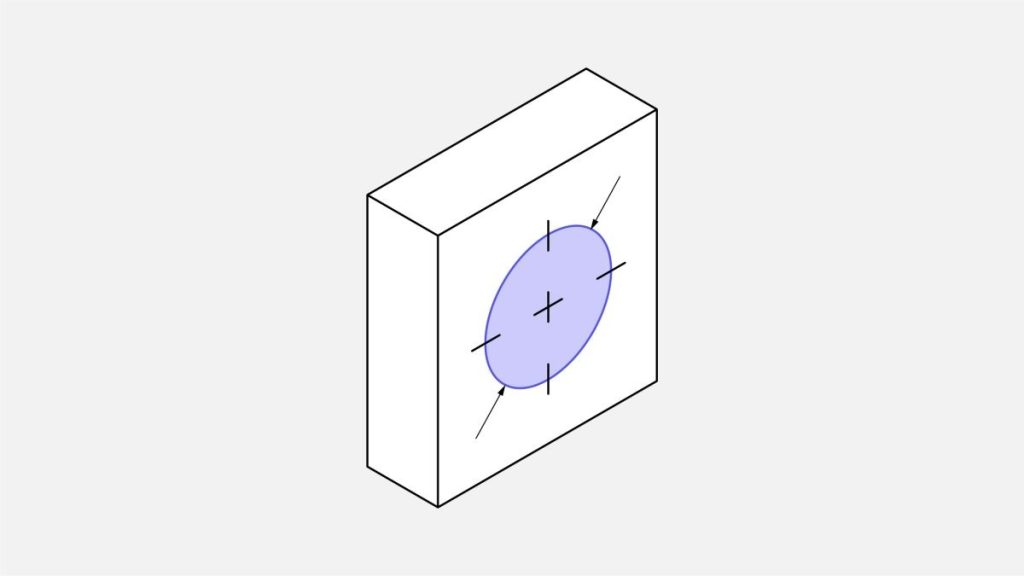
Only specify tolerances when necessary
It is recommended to only establish narrow tolerances during machining when absolutely necessary, as doing so can increase costs. In the absence of a specified tolerance on the technical blueprint, components are machined with the standard tolerance (± 0.125mm or superior), which is generally suitable for non-critical features.To minimize cost:
Only establish stricter tolerances when it is absolutely essential. Establish a solitary datum (such as the intersection of two edges) as a point of reference for all dimensions with tolerances.
Geometric Dimensioning and Tolerancing (GD&T) can be employed in technical sketches to reduce the costs associated with CNC machining. GD&T covers various characteristics such as flatness, straightness, circularity, and true position, which aid in achieving this objective. It commonly establishes a broader tolerance, yet demands a sophisticated understanding of design for efficient implementation.
Minimize the number of machine setups
Develop components that can be produced with minimal machine configurations, ideally necessitating just a single setup. For instance, if a component features blind holes on both sides, it would typically necessitate two setups as it needs to be rotated to access both sides.Repositioning or rotating a component leads to increased production costs, often requiring manual intervention. Additionally, complex shapes may demand a specialized fixture, leading to additional costs. Particularly intricate shapes may call for a multi-axis CNC system, further driving up expenses.
It is advisable to divide the section into several geometries that can be CNC-machined in a unified setup and subsequently joined through bolting or welding. This suggestion can also be implemented for parts with very deep pockets. To reduce expenses, create components with basic 2.5D shapes that can be produced in one CNC machine setup. If this is not feasible, divide the part into various geometries that can be joined together at a later stage.
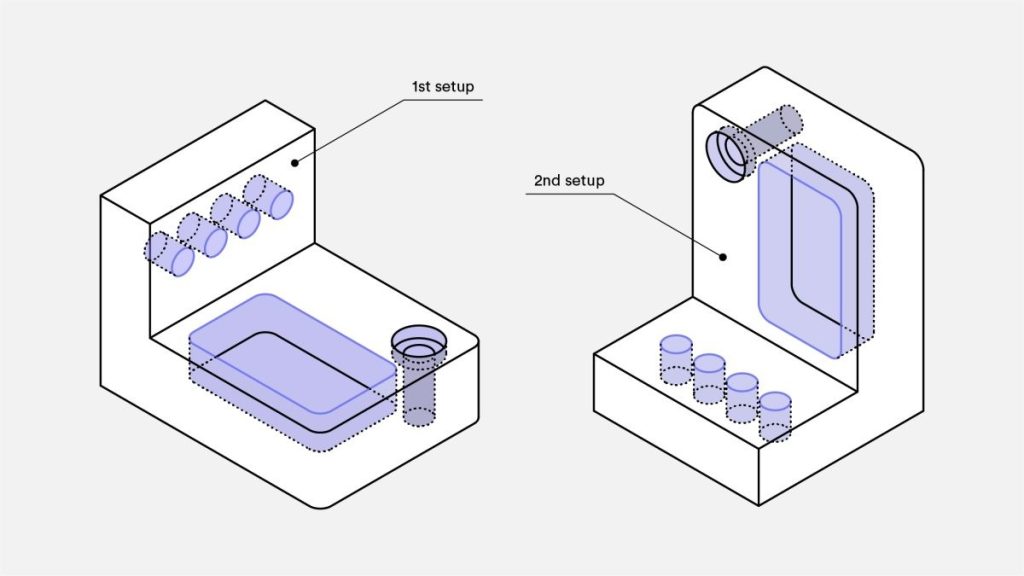
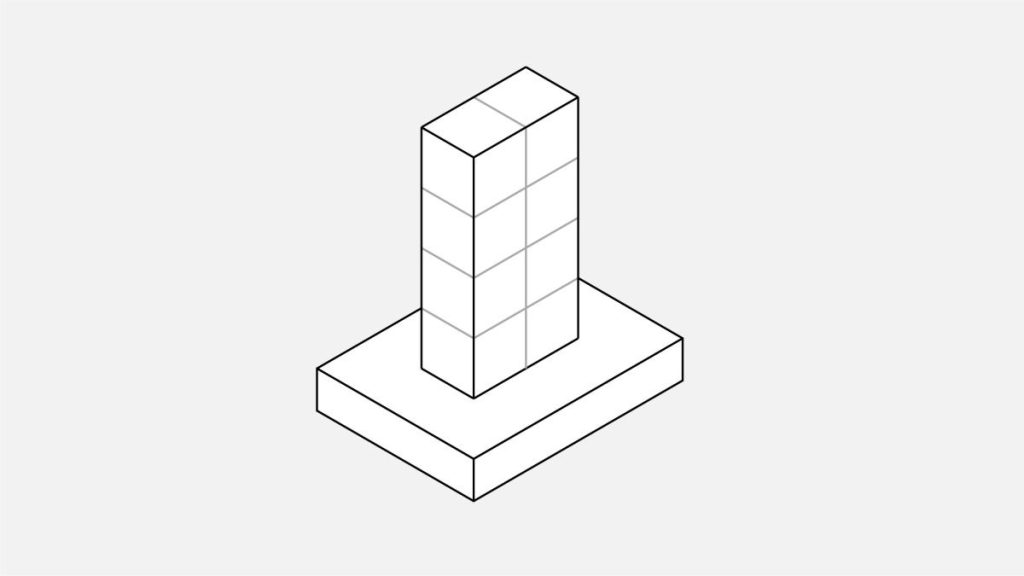
Avoid small features with high aspect ratio
Features that are small and have a high width-to-height aspect ratio are susceptible to vibrations, making them difficult to machine with precision.
To minimize cost:
Design features that have a width-to-height aspect ratio of less than four should be considered.It is recommended to add bracing support or connect these smaller features to a wall in order to improve their stiffness.
Remove all text and lettering
Adding text to the surface of a CNC-machined part can significantly raise costs as it requires additional machining operations, leading to extended production durations. Utilizing surface finishing techniques like silk screening or painting presents a more economical approach to incorporating text on a CNC-machined part.
To minimize cost:
Remove all text and markings from your CNC-machined components. If text is necessary, choose engraved lettering instead of raised lettering.
Utilize a minimum of size-20 sans serif font (such as Arial or Verdana).
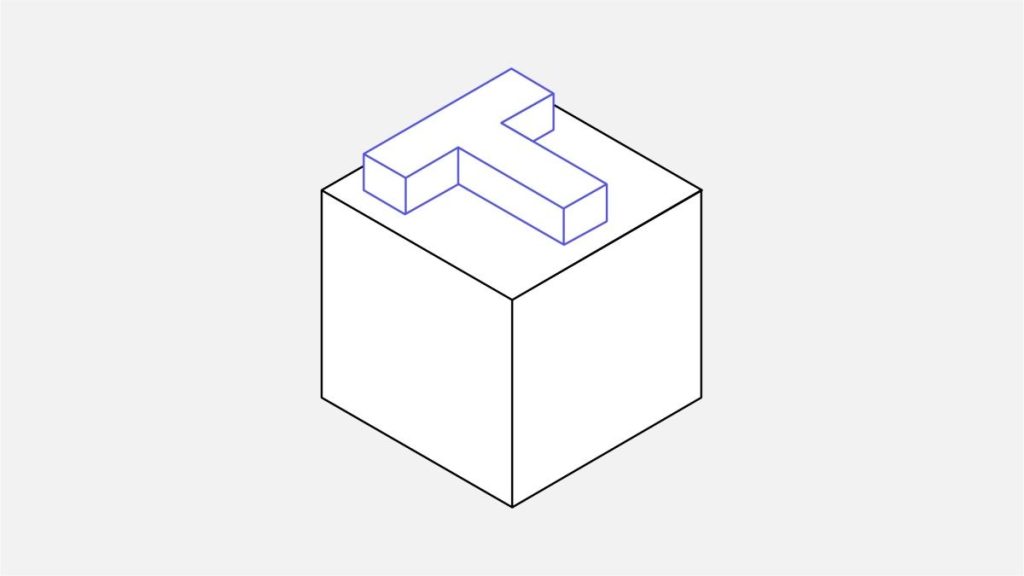
Consider the machinability of the material
Geometric Dimensioning and Tolerancing (GD&T) can be employed in technical sketches to reduce the costs associated with CNC machining. GD&T covers various characteristics such as flatness, straightness, circularity, and true position, which aid in achieving this objective. Machinability is influenced by the physical characteristics of the material. In general, metals that are more malleable and flexible are easier to work with using machining techniques. Among various alloys, C360 brass stands out for its exceptional machinability, allowing for high-speed machining. While aluminum alloys like 6061 and 7075 can also be machined easily, they require slightly lower speeds. On the other hand, stainless steel has a machinability that is 10 times lower than aluminum, resulting in a machining process that takes at least twice as long. The machinability of stainless steel varies depending on the grade. For example, 304 stainless steel has a machinability index of 45 percent, while 303 stainless steel, which has a similar chemical composition, boasts an index of 78 percent, making it more suitable for machining.When it comes to plastics, their machinability primarily depends on their thermal characteristics and rigidity, as they are prone to melting and deformation during the machining process. POM (Derlin) is considered the most easily machinable plastic, closely followed by ABS. However, common engineering plastics like PEEK and nylon 6 present more challenges when it comes to machining.To minimize costs, it is advisable to choose materials with superior machinability, especially for bulk orders.
Consider the price of the bulk material
The price of CNC-machined parts can be greatly influenced by the cost of the bulk material. The provided table offers a summary of the prices for metal alloys and plastic materials commonly used in CNC machining for a sheet that measures 6″ x 6″ x 1″ (or approximately 150 x 150 x 25mm). Aluminum 6061 is the most cost-effective choice for creating metal prototypes due to its affordability and excellent machinability. However, metals such as stainless steel 303 and C360 brass, which have improved machinability, come at a higher price and are therefore more suitable for larger scale manufacturing. In such scenarios, the concept of economies of scale becomes significant as the increased material cost is offset by significantly reduced machining times.
In terms of plastics, ABS, nylon, and POM (Derlin) are priced similarly to aluminum 6061. However, due to their challenging machinability, a higher cost should be anticipated. On the other hand, PEEK is an exceedingly costly material that should be reserved for essential applications.
To minimize cost:
Choose a material with low bulk price, especially for low-volume orders.
Avoid multiple surface finishes
Surface finishes not only improve the visual appeal and longevity of CNC-machined parts but also come at a higher cost. The expenses rise even more when multiple surface finishes are required for one component, as it involves extra steps like surface masking.For a comprehensive overview of the advantages offered by various surface finishes for CNC parts, please refer to the following article.
To minimize cost:
Select the surface finish that is in its original state after machining.
Request multiple surface finishes only in cases of absolute necessity.
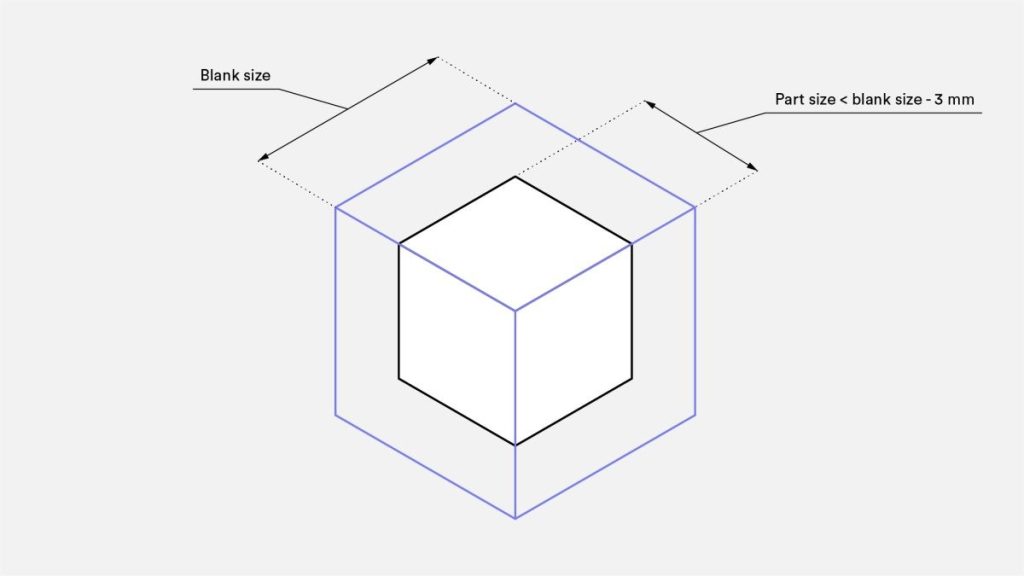
Account for blank size
The total expenses can be influenced by the dimensions of the void or the raw material. Typically, the void should exceed the final part by at least 3mm. Precision is upheld by carefully trimming material from all edges of the part.The total expenses can be influenced by the dimensions of the void or the raw material.Typically, the void should exceed the final part by at least 3mm. The accuracy is upheld by removing excess material from all sides of the component.
To minimize cost:
Design components with dimensions that are 3mm less than the standard blank size.
Take advantage of economies of scale
The unit price in CNC machining is greatly impacted by the order quantity. This is because of the relatively high initial costs, which make up a significant portion of the total cost for small orders. On the other hand, for larger orders, the cost per unit decreases.
Below, we present a graph illustrating the mean unit price of 12 distinct components that have been machined using stainless steel 304.
The decrease in unit price follows an almost exponential pattern, indicating that a mere increase in volume from one to five can result in a 50% reduction in the unit price. Furthermore, placing orders for significantly large volumes (over 1,000 parts) can lead to a five to tenfold decrease in the unit price.To minimize cost:Take advantage of economies of scale by ordering higher quantities.
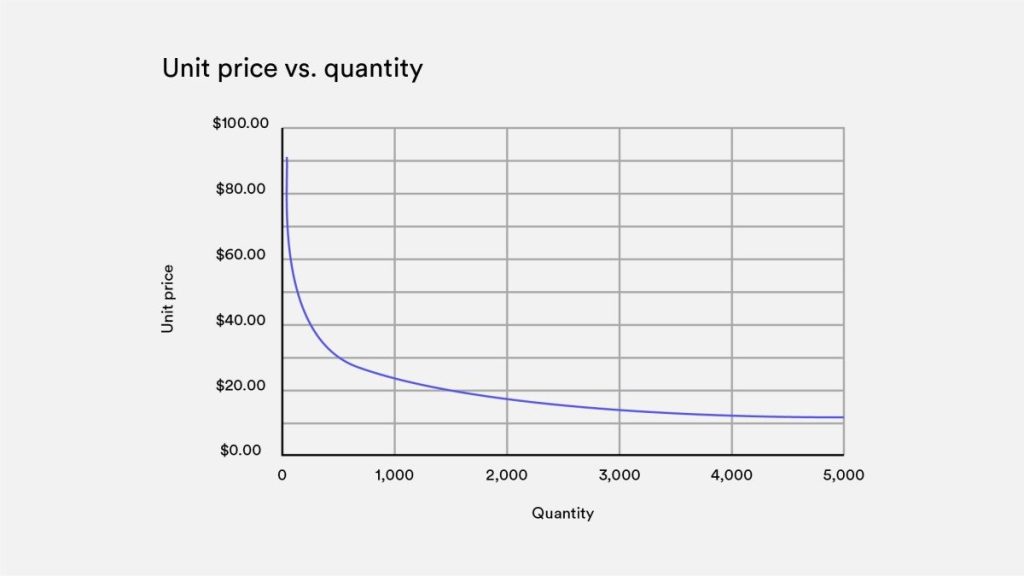
Best practices for lowering CNC costs
CNC operations
In conclusion, keep your CNC machining simple.
CNC operations come with a hefty price tag when dealing with intricate designs. Additional expenses are incurred when dealing with geometries that require specific tooling or fixtures, multiple machine setups, or specialized materials.
So to keep costs down, before you submit an order for quoting, ask the following questions:Has my part been optimized according to machinability guidelines during the design process?Are all the features in my model essential, or can some be eliminated or simplified without affecting the part’s functionality?
Is it feasible to break down my design into several components in order to facilitate CNC machining and assembly? Can adjustments be made to the design to eliminate the need for multiple machine setups or specialized tooling? Are there alternative materials that are more cost-effective or easier to machine while still meeting the design requirements?
The present & the future of CNC machining
CNC tooling
The potential of CNC machining is continuously growing. For instance, the latest advancements in CNC tooling allow contemporary CNC systems to thread holes along their entire length. Moreover, CNC machines can effortlessly fabricate holes of any size without a substantial impact on the cost. This is achieved by utilizing a plunging CNC tool and employing profile interpolation, which involves following a helical tool path.
In this article, our main emphasis was on providing general guidelines for designing with manufacturability in mind, which can be applied universally regardless of the CNC system being utilized. Consider these tips as valuable practices that can enhance your efficiency in designing parts.