Metalworking, particularly milling, is extensively utilized in contemporary prototyping methods. Manufacturers of prototypes aim to optimize the functionalities of their equipment in relation to technology. Spiral milling has emerged as a prominent technique in recent times. It is essential to comprehend the concept of spiral milling, its benefits and drawbacks, and how this information can be leveraged in prototype design to minimize production expenses.abs cnc machining
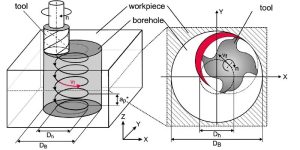
Table of Contents
What is spiral milling?
Spiral milling presents itself as an alternative method for hole machining. By employing an end mill along a spiral path, this technique ensures the creation of top-notch holes. It offers numerous benefits compared to traditional drilling and can effectively replace the need for boring machines. This proves particularly advantageous for prototyping workshops aiming to minimize equipment expenses. Spiral milling proves versatile, capable of processing various hole types, while also reducing cutting forces, minimizing tool wear, and delivering commendable quality.cnc machining shenzhen
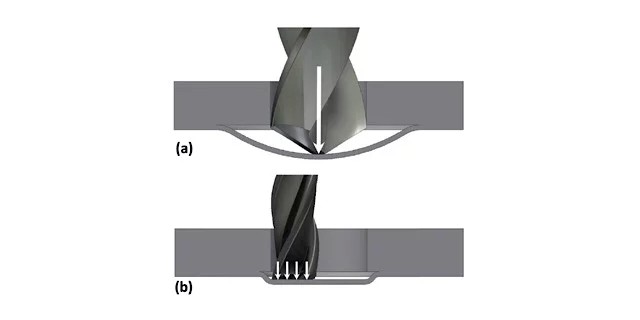
Why not drill a hole?
The primary alternative to spiral milling is traditional drilling, a widely used method for creating holes. Data shows that in the production of metal components, drilling constitutes 25% of the cycle time and 33% of all processing operations. However, why should milling be taken into consideration? Despite its simpler kinematics, drilling comes with several drawbacks, necessitating the adoption of more intricate milling techniques.cnc machining 800
For instance, the drilling speed varies depending on the diameter, being highest at the periphery and nearly zero at the center of the bit. Consequently, the machining process near the rotational axis involves plastic deformation rather than cutting. This leads to increased tool thrust and rapid tool wear.inconel cnc machining
As a result of axial thrust, a bit (especially a worn one) causes metal to bend as it exits the workpiece. The excess material protruding around the hole must be manually removed. The utilization of a milling machine can significantly reduce the leftover material.cnc machining bushing
Drilling underperforms in terms of chip removal, leading to negative impacts on surface finish and cutting temperature. The removal of processed material is solely dependent on drilling grooves, which in turn affects the quality of the hole’s surface finish. Metal fragments carried by chips scratch the hole’s sides, further deteriorating the surface finish. Additionally, chips carry a significant amount of cutting heat, contributing to increased bit temperature and faster wear. To address these issues, operators opt for a discrete drilling method, where the drill machines a section of the length before removal. While this method is effective in improving chip removal, it results in longer drilling times. In light of these drawbacks, manufacturers turn to spiral milling to enhance process efficiency and overall shop productivity.cnc hardware machining
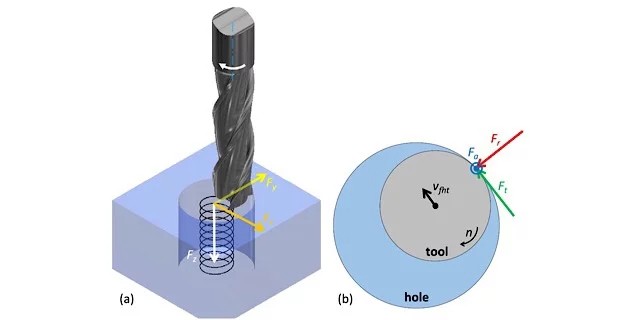
Some spiral milling details
Let us examine several of the procedures involved in spiral milling.cnc machining flanges
To begin, the end mill follows a spiral trajectory. This implies that the milling center must integrate vertical Z-axis movement with horizontal xy-axis movement. Consequently, manually composing NC programs for this process can be quite intricate. However, numerous CAM systems have embraced spiral milling as a viable strategy.bike cnc machining
The chip geometry encompasses two distinct regions: the blue area formed by the side of the end mill and the red area formed by the surface of the mill. Research has demonstrated that the proportion between these two regions is solely determined by the tool and the aperture. paint cnc machining
As the diameter of the tool increases, the blue area increases. Unlike red chips, since blue chips are discontinuous, it provides worse milling in terms of vibration. As a result, the surface finish will deteriorate. In addition, as the volume removed from the sides of the milling cutter increases, the radial cutting forces increase (red Fr in the figure) and they bend the tool inside the hole, so the tolerance decreases. Since larger tools have greater rigidity, negative effects are reduced to a certain extent.part machining cnc
If the tool is smaller, the red region is dominant, so the radial force is smaller and the vibration is also smaller, but the reduction of the tool diameter is limited by the stiffness of the system.I would say it’s better to start with a larger tool and then change it to a smaller tool for a final cut with low depth and feed for an excellent surface finish.stell machining cnc
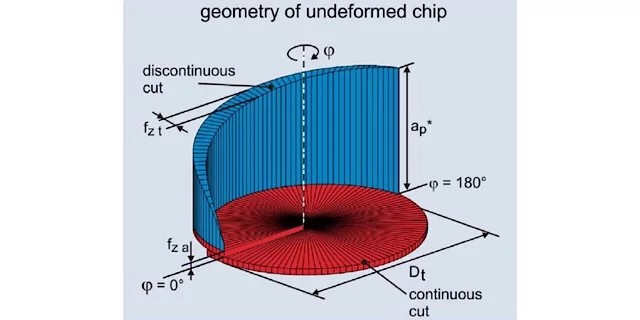
Reasons for using spiral milling
As you can see, spiral milling is a promising process with many advantages.cnc machining wood case
You can achieve any diameter with improved precision and surface quality without the need to switch tools.cnc machining parts=feed When drilling a hole larger than 35 mm, using a single bit is not the best choice.cnc machining precision parts Typically, this process involves using a series of smaller bits, starting with a 10 mm bit, then moving to 20 mm, and finally reaching 35 mm.cnc custom machining part If higher precision or surface finish is required, you can ream or countersink the hole, eliminating the need to switch between 4-6 tools.die castings cnc machining By utilizing spiral milling, you can simply use an end mill to create the hole and adjust the feed rate for the desired tolerance and quality. With Ra 1.25, you can achieve up to IT7 without tool changes.spline manufacturing cnc machining
Lower cutting temperatures and improved chip removal are achieved with this method.carbon fiber cnc machining The end mill does not fully occupy the hole, which is the primary benefit.cnc machining metal block There is no need to constantly remove the tool every 30 mm or so after cutting.vertical cnc machining centre auto cnc machining parts Instead, simply spray coolant into the hole to eliminate chips and lower the processing temperature.phone holders cnc machining
Lower cutting temperatures and improved chip removal are achieved with this method.proto type cnc machining The end mill does not fully occupy the hole, which is the primary benefit.vertical machining center cnc There is no need to constantly remove the tool every 30 mm or so after cutting.cnc machining centre parts Instead, simply spray coolant into the hole to eliminate chips and lower the processing temperature.custom cnc machining service
conclusion
Spiral milling is indeed an innovative process with its own set of limitations.cnc machining parts precision One such drawback is the relatively slow chip removal and the lack of thorough research on its parameters.cnc machining ar parts Nevertheless, this method streamlines the number of settings, machining steps, and tools needed, all while upholding the integrity of the hole being created.machining services cnc shop This proves to be a significant advantage for prototype manufacturers aiming to reduce the amount of tools and equipment necessary for their projects.aluminum parts cnc machining