Table of Contents
Why are sharp corners an issue in CNC machining?
tooling radius
The machinist’s choice of tooling radius in the CNC process directly impacts the achievable corner radii and the overall quality and efficiency of the produced parts. The minimum internal sharp corner radius that can be achieved with CNC is limited by the radius of the cutting tool. Attempting to create sharp corners with a 90-degree path is not feasible with CNC tools. If one still tries to do so, it will necessitate stopping the machine and adjusting the workpiece, leading to potential chatter marks, increased vibration, slower machining, and ultimately, subpar part production.
the importance of avoiding sharp corners
sharp corners
Have you incorporated sharp corners into your parts? While they may appear visually appealing on paper, they pose significant challenges when it comes to CNC machining. Discover in this informative article the importance of avoiding sharp corners in your designs, as it can effectively minimize lead times, costs, and potential difficulties for machinists.
sharp corners in CNC machining
Sharp internal corners pose a significant challenge for CNC machinists. The cutting tools commonly used in CNC machining, such as end mills and drills, are cylindrical in shape with limited cutting lengths. As a result, these tools will always create a radius when cutting an internal pocket, based on the geometry of the tool itself. Consequently, parts manufactured using CNC machines will inevitably feature at least a small radius, complicating the production of designs with sharp corners. While there are techniques available for machining sharp corners, they tend to be costly. Therefore, we advise incorporating sharp corners into your design only if absolutely necessary and justifiable in terms of additional production expenses. This article delves into the reasons behind the challenges posed by sharp corners in CNC machining and provides guidance on how to address this issue in your design.
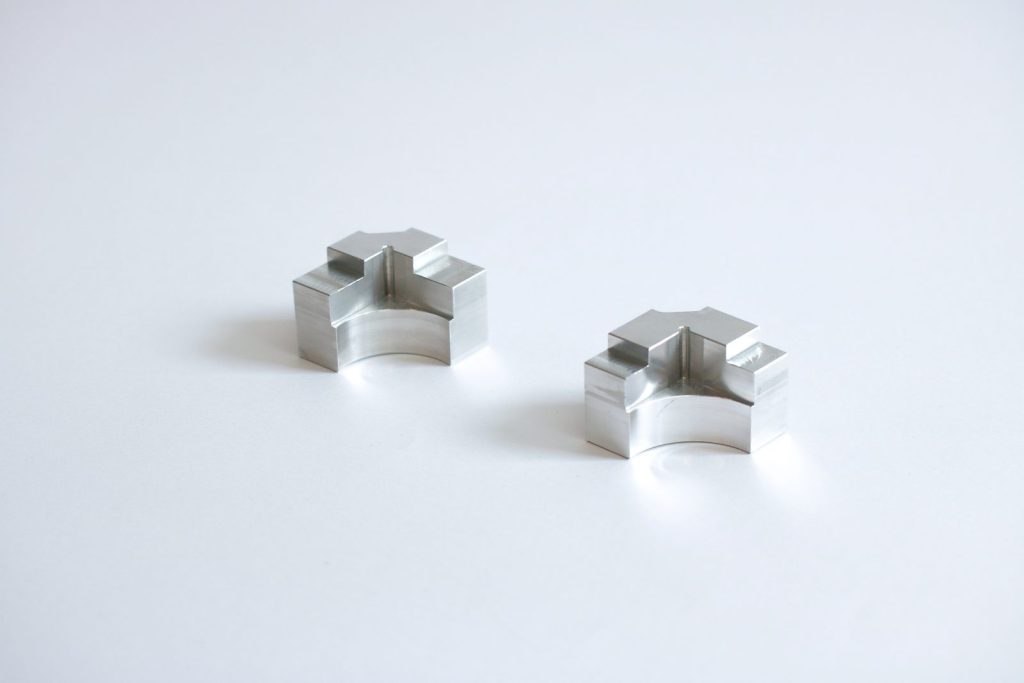
When and how to add a corner radius (or fillet)
Increasing the radius
Increasing the radius of your part’s corners is the initial step to address the issue of internal sharp corners. Larger tools can create bigger corner radii, leading to faster machining times. However, this may result in rougher surfaces. The tool radius is also connected to the depth of pockets. Using a smaller diameter tool on deep pockets can cause vibrations, resulting in chatter marks and tool fatigue. A general guideline is to ensure that the radii at the corners are at least 1/3 of the cavity depth, with the cavity depth being two to three times the cutter’s diameter. It is essential to remember that although this method is straightforward, it can be quite expensive.
How do you solve the sharp corner problem for CNC machinists?
incorporating fillets
There are numerous approaches to address the issue of sharp corners, which include incorporating fillets and altering the technologies employed in the production of customized components.
When and how to use T-bone and dogbone fillets
curved internal corners
When components require assembly, curved internal corners can present challenges during the fitting process. This is where dogbone and T-bone fillets prove to be useful.
Sharp internal corners pose a significant challenge for CNC machinists. The cutting tools commonly used in CNC machining, such as end mills and drills, are cylindrical in shape with limited cutting lengths. As a result, these tools will always create a radius when cutting an internal pocket, based on the geometry of the tool itself. Consequently, parts manufactured using CNC machines will inevitably feature at least a small radius, complicating the production of designs with sharp corners. While there are techniques available for machining sharp corners, they tend to be costly. Therefore, we advise incorporating sharp corners into your design only if absolutely necessary and justifiable in terms of additional production expenses. This article delves into the reasons behind the challenges posed by sharp corners in CNC machining and provides guidance on how to address this issue in your design.
T-bone fillets
A single T-bone fillet elongates the corner in a singular direction. The cutting tool extends the corner of its tool radius, enabling a complementary component to possess a precise corner.
Dogbone fillets
Dog-bone fillets, as their name implies, resemble chew toys for canines. These fillets extend the corner in two directions, enabling a perfect fit with a mating part, even if it possesses a sharp corner. This design aids in distributing the removed material on both sides of the corner, resulting in a stronger overall structure. While this solution is simple and effective, it does entail the removal of more material than required.
A more elegant and inconspicuous approach involves placing a two-directional dogbone at a distance of √(R² / 2) from the corner itself. This positioning allows for the complete machining of the corner’s occupied area, without the unnecessary removal of excess material.
When and how to use EDM (electrical discharge machining)
Electrical discharge machining, commonly referred to as spark machining or arc machining, is a distinctive manufacturing technique that eliminates material from a workpiece through a sequence of repetitive electrical discharges. Material is removed from the workpiece to achieve precise part dimensions as current passes between two electrodes separated by a dielectric liquid.
There are two different types of EDM:
Sinker EDM, also known as ram EDM, comprises an electrode and workpiece that are submerged in an insulating liquid, such as oil or other dielectric fluids. Both the electrode and workpiece are connected to an appropriate power supply, which generates an electrical potential between the two components. As the electrode gets closer to the workpiece, the dielectric fluid experiences a breakdown, creating a plasma channel for small sparks to leap across.
Advantages of EDM:
Capability to fabricate intricate forms
The hardness of the material has no impact on the procedure
Inner profiles and inner corners as small as R0.02 mm
Absence of direct interaction between the tool and the workpiece enables machining of fragile sections and delicate materials without noticeable deformation.
Disadvantages of EDM:
The sluggish pace of material elimination
Limited to machining conductive materials exclusively
The supplementary time and expenses involved in fabricating electrodes for ram/sinker EDM
High power consumption
Poses challenges for machinists and entails significant costs
The resulting surface texture tends to be rough, necessitating post-processing for any machined area.