This article explores the different types of heat treatment and how they affect CNC-machined components. It explains how heat treatments can improve important physical properties like hardness, strength, and machinability in a variety of metal alloys.Heat treatment is a procedure that involves exposing metal alloys to high temperatures, followed by controlled cooling.custom cnc laser cutting machining service The specific temperature, heating duration, and cooling rate all play a crucial role in determining the final physical properties of the alloy.cnc machining parts aluminum stainless steel Through heat treatment, metal alloys can undergo significant enhancements in characteristics such as hardness, strength, and machinability.cnc machining stainless steel turning part These improvements occur due to alterations in the microstructure and, in some instances, the chemical composition of the material.This article offers an overview of the different heat treatment techniques suitable for commonly used metal alloys in CNC machining, assisting in the selection of the most appropriate material for specific applications.metal machine precision custom cnc machining
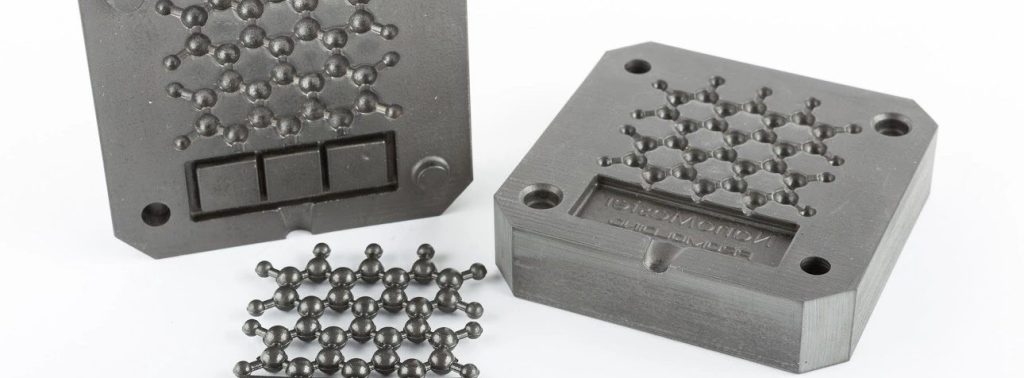
Table of Contents
Heat treatment in CNC machining
process
the most suitable heat treatment
- The process of heat treatment is essential in the CNC machining of metal parts as it involves precise management of the heating and cooling phases to achieve specific material properties, influencing the hardness, strength, toughness, and ductility of the components.cnc parts milling and turning machining service
- The choice of the most suitable heat treatment technique relies on various factors including the composition of the material, the size of the part, and the desired material properties.cnc lathe center machining, aluminum parts process The primary objective of heat treatment is to achieve a particular microstructure that enhances the desired characteristics of the parts.parts 5 axis cnc machining custom aluminum parts
- involves the process of heating and cooling metal materials in order to alter their physical and mechanical properties.5 axis cnc metal machining milling stainless
What is the appropriate timing to implement heat treatments on metal components?
Heat treatments may be utilized on metal alloys at different points during the CNC machining process, whether it occurs before initiating the machining of components or following it.cnc machining cnc machining
Before CNC machining
The CNC service provider will fabricate the parts directly from the readily available stock material when there is a request for a standardized grade of a metal alloy. Opting for this approach is frequently the most effective way to minimize lead times.
After CNC machining
Certain heat treatments can greatly enhance the hardness of a material or serve as a final step following the forming process. In such instances, the heat treatment is implemented post CNC machining, as heightened hardness can hinder the machinability of the material. This procedure is commonly adopted when CNC machining tool steel components.
What are common heat treatments for CNC materials?
heat treatments
Annealing, tempering, and stress relieving are thermal processes used to treat metal alloys.cnc turning machining parts Each process involves heating the alloy to a specific temperature and then cooling it gradually.aluminum cnc machining service The key distinction between these processes lies in the temperature at which the material is heated and the sequence in which they are performed during manufacturing.cnc machining formal During annealing, the metal alloy is subjected to an extremely high temperature and then slowly cooled.most complicated cnc machining This technique is typically applied to all metal alloys after their formation and before any further processing occurs.cnc lathe machining service The primary objective of annealing is to soften the metal and improve its machinability.cnc titanium turning machining In the absence of any other specified heat treatment, most CNC machined parts will possess the material properties of the annealed state.cnc machining roland On the other hand, stress relieving involves heating the part to a high temperature, albeit lower than that used in annealing.cnc machining lathe parts This process is usually conducted after CNC machining to eliminate any residual stresses that may have been generated during the manufacturing process.
Tempering
cnc machining poliuretano By doing so, parts with more consistent mechanical properties can be produced.Tempering is a different procedure that requires heating the component, albeit at a lower temperature compared to annealing.cnc vertical machining center torn This method is frequently utilized following the quenching of mild steels (e.g. 1045 and A36) and alloy steels (e.g. 4140 and 4240).abs machining turning milling cnc The purpose of tempering is to decrease the brittleness of these steels and enhance their general mechanical properties.cnc machining aluminum case
Quenching
The process of quenching involves subjecting the metal to intense heat, followed by a rapid cooling technique such as immersion in oil or water, or exposure to a cool air stream.aluminum cnc machining wheel spacer This rapid cooling effectively preserves the changes in the microstructure that occur during heating, resulting in components with exceptional hardness.mini cnc k4040t machining
Typically, components undergo quenching as the final step in the manufacturing process, especially after CNC machining.cnc machining car body kit This is similar to how blacksmiths immerse their blades in oil.cnc machining sheet metal spinning The increased hardness achieved through quenching makes the material more resistant to machining.
In the case of tool steels, quenching is performed after CNC machining to achieve a high surface hardness.custom cnc machining services stainless Subsequently, a tempering process may be used to regulate the hardness.carbon steel parts cnc machining service For example, Tool steel A2 exhibits a hardness of 63-65 Rockwell C after quenching, but it can be tempered to achieve a hardness ranging from 42 to 62 HRC.logo engraving steel cnc machining parts Tempering improves the longevity of the part by reducing brittleness, with optimal results obtained at a hardness of 56-58 HRC.
Precipitation hardening (aging)
Precipitation hardening and aging are two terms frequently employed to depict the identical process.titanium cnc machining milling turning parts The process of precipitation hardening involves three steps: first, the material is exposed to high temperatures, then rapidly cooled, and finally heated to a lower temperature for a longer period of time (aged).metal spare parts cnc machining manufacturer This causes the alloy elements, which were initially separate particles with different compositions, to dissolve and evenly disperse throughout the metal matrix, similar to how sugar crystals dissolve in heated water.
As a result of precipitation hardening, the strength and hardness of the metal alloys significantly increase.customized high quality oem cnc machining service For example, the aluminum alloy 7075, widely used in the aerospace industry, can produce components with tensile strength comparable to stainless steel, while weighing less than three times as much.The impact of precipitation hardening on aluminum 7075 is illustrated in the table below:This method of heat treatment is not applicable to all metals; however, the metals that can undergo this process are known as superalloys and are ideal for extremely high-performance applications. Below, you will find a summary of the most frequently used precipitation hardening alloys in CNC.
Case hardening & carburizing
Case hardening refers to a range of heat treatments that yield components with high hardness, while maintaining the softness of the underlying materials. This approach is often favored over uniformly increasing the hardness of the entire part (e.g., through quenching) since excessively hard parts tend to be more brittle.
Among the various case-hardening techniques, carburizing is the most commonly employed heat treatment. It entails subjecting mild steels to elevated temperatures in an environment rich in carbon, followed by rapid cooling to trap the carbon within the metal matrix. This process enhances the surface hardness of steels in a manner akin to how anodizing enhances the surface hardness of CNC aluminum parts.
How to specify a heat treatment on CNC orders with Protolabs Network
When submitting a CNC machining order, there are three methods available to request a heat treatment:
Referencing a manufacturing standard: Numerous heat treatments are standardized and commonly employed. For example, the T6 label found in aluminum alloys such as 6061-T6, 7075-T6, and others signifies that the material has been subjected to precipitation hardening.custom high precision cnc machining aluminum parts
Specify the required hardness
This is a widely used approach for specifying the heat treatment of tool steels and case hardening. It provides clear instructions to the manufacturer regarding the necessary heat treatment process after CNC machining. For instance, in the case of D2 tool steel, it is customary to specify a desired hardness range of 56-58 HRC.
Specify the heat treatment cycle
Once the details of the necessary heat treatment are determined, they can be conveyed to the supplier during the order placement process. This enables you to tailor the material properties to suit your specific application. Naturally, this task demands a profound understanding of metallurgy. Rest assured, we are here to assist you with all of these requirements.