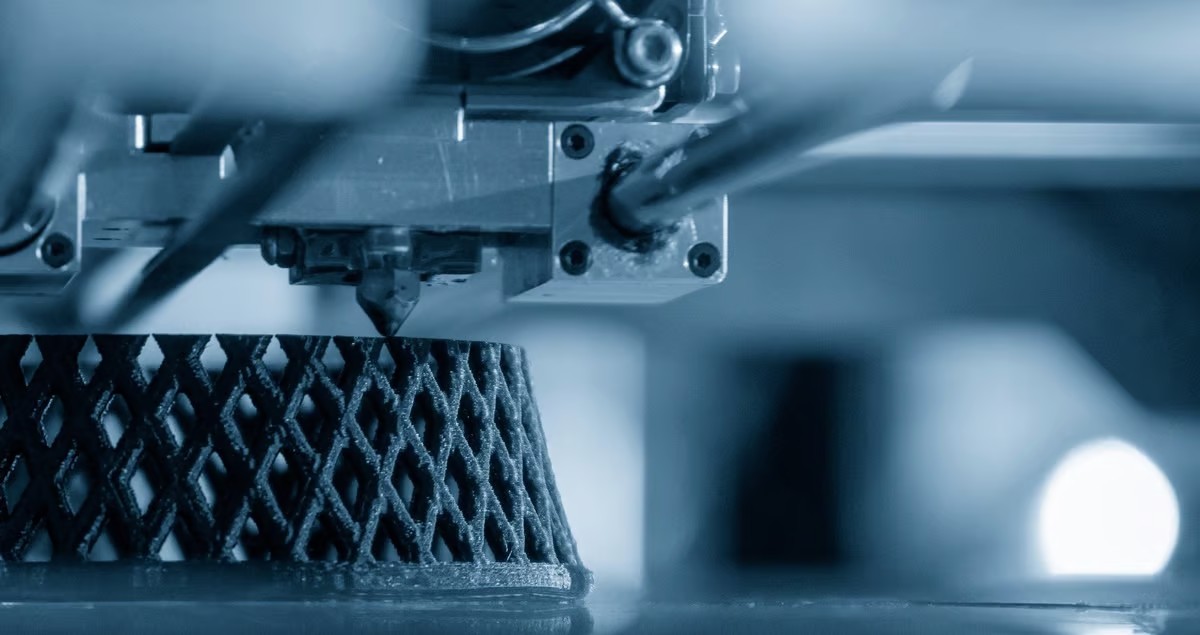
Rapid Prototype Services
- Product design and rapid prototyping for manufacturing
- Rapid prototype development
- Industries using rapid prototyping
- Types of rapid prototyping
- Benefits of rapid prototyping
- Customers using rapid prototyping
What is rapid prototyping?
Rapid prototyping often utilizes 3D printing to swiftly produce scale models or assemblies according to digital designs, typically sourced from 3D CAD files. The capacity to promptly create and enhance physical prototypes allows engineers to receive valuable input from colleagues in an efficient and economical way. Industrial designers and associates might employ rapid prototyping to assess aesthetics and ergonomics for user testing, while engineers could offer insights on a prototype’s material characteristics and functionality. Additional team members may verify the rapid prototypes for manufacturability and usability beforehand.
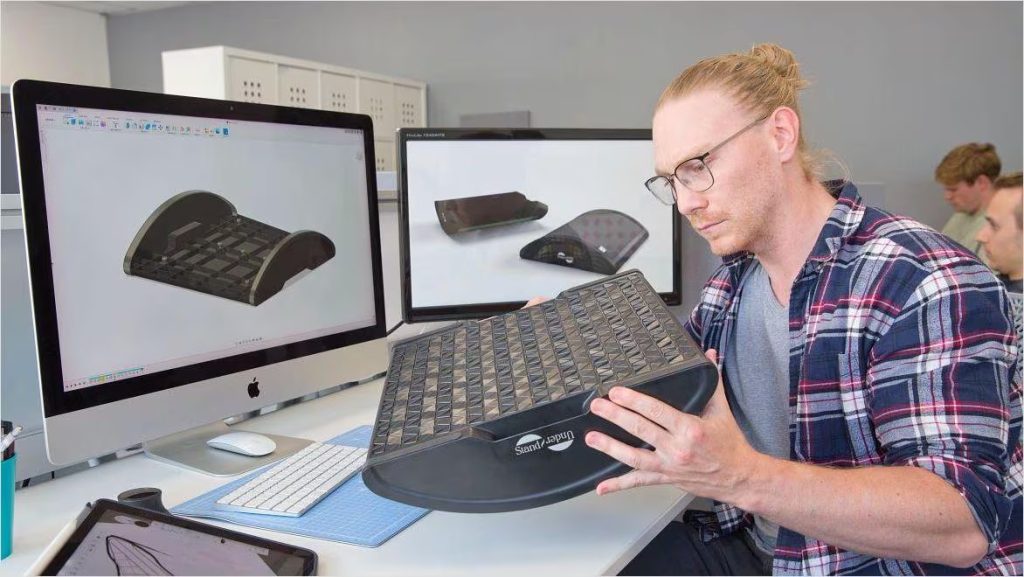
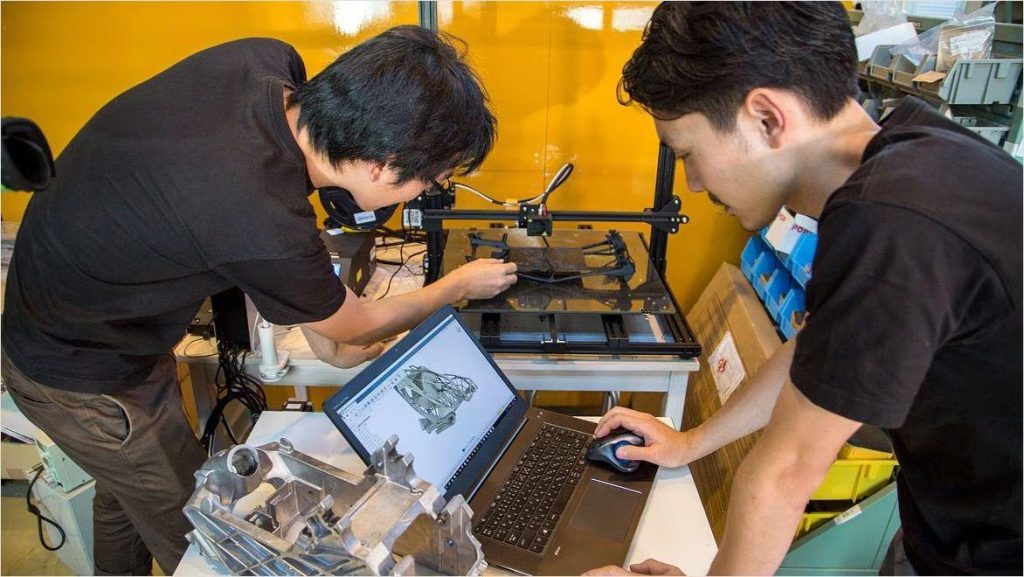
Product design and rapid prototyping for manufacturing
Rapid prototyping is now an essential part of product design, enabling the quick transformation of digital ideas into physical models. This rapid process allows for immediate feedback, which helps to pinpoint any design flaws and ensures a smoother transition from concept to production.
Additive manufacturing, also known as 3D printing, has transformed rapid prototyping by offering a cost-effective and efficient way to create intricate designs. Its user-friendly approach speeds up the prototype development process, allowing designers to make changes quickly and address design challenges promptly.
In addition, CNC machining enhances rapid prototyping by providing precise results and specific surface finishes, particularly for components that require tight tolerances or specific materials. This method combines speed and accuracy to ensure that prototypes are both functional and polished.
Rapid prototype development
With the utilization of in-house 3D printers, the process of rapid prototyping can be condensed into a 24-hour cycle. During the workday, designers focus on developing a 3D CAD model, which is then printed overnight to create the prototype parts. The following day, the prototype’s design is tested and adjusted accordingly. This efficient workflow allows engineering teams to incorporate valuable feedback from clients and collaborators, bringing each iteration closer to the final product’s desired form. By identifying and resolving design issues early on, this feedback cycle aids developers in preparing for production runs. Moreover, the ability to test numerous product iterations empowers engineers to explore various design concepts with minimal risk. The development of rapid prototypes can encompass multiple stages, wherein the prototype evolves in complexity and physical properties. In the initial stages of product development, proof-of-concept (PoC) prototypes serve to validate concepts and demonstrate the feasibility of a product. Looks-like prototypes showcase the ergonomics and user experience of a potential final product, even if they do not possess complete functionality. Works-like prototypes, on the other hand, may not resemble the final product visually, but they exhibit the same mechanical, thermal, and electrical functionality and properties. Lastly, engineering prototypes combine the characteristics of looks-like and works-like prototypes to create a final preproduction prototype that is suitable for manufacturing (DfM) and minimally viable for laboratory testing.
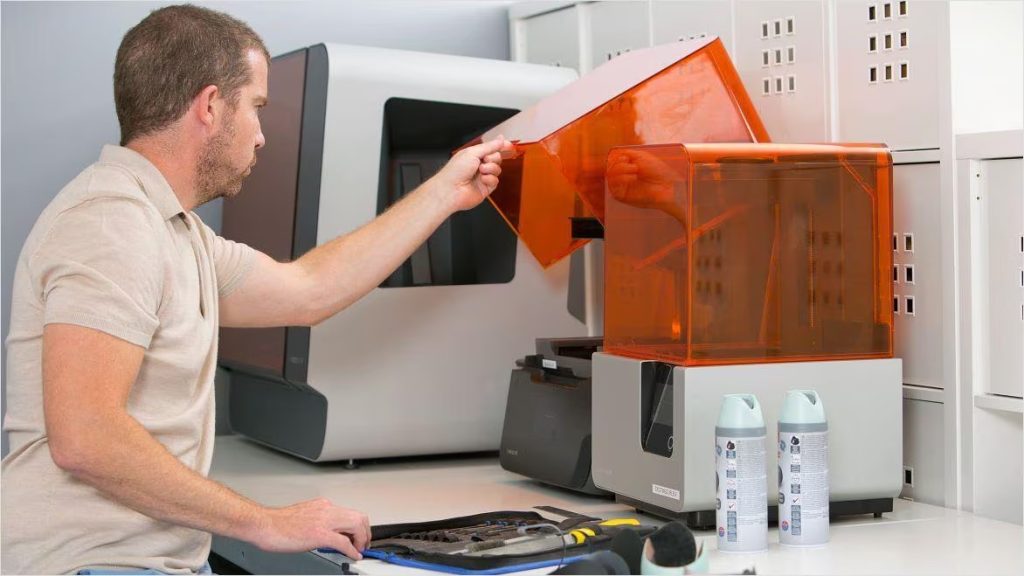
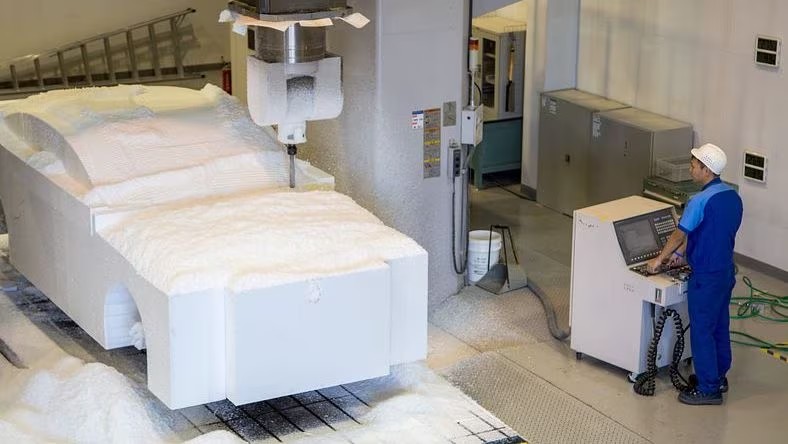
The automotive industry has been at the forefront of rapid prototyping and still heavily relies on it for the development of parts and vehicle concepts.
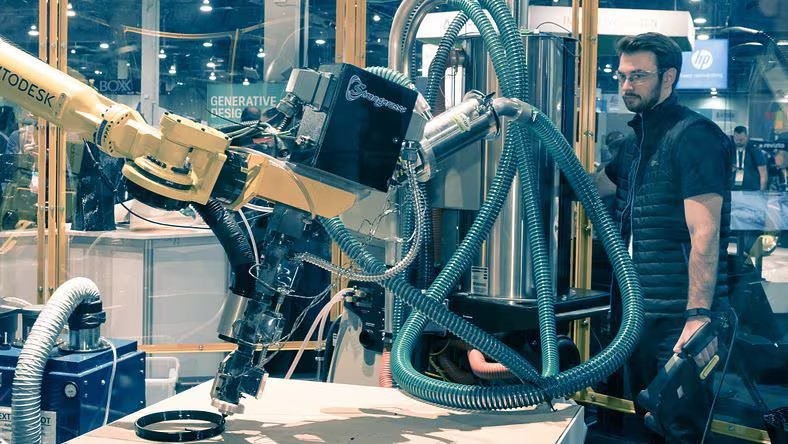
Rapid prototyping is also responsible for manufacturing the tools required for creating prototypes. In situations where industrial processes require unique tools or customized parts such as injection molds, rapid prototyping, also known as “rapid tooling,” proves to be beneficial.
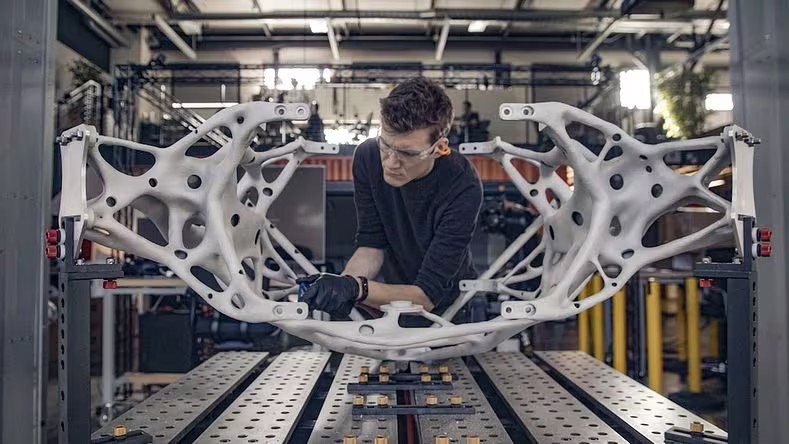
Rapid prototyping plays a crucial role in the aerospace industry by facilitating the development of components, structures, and concept designs for both aircraft and spacecraft.
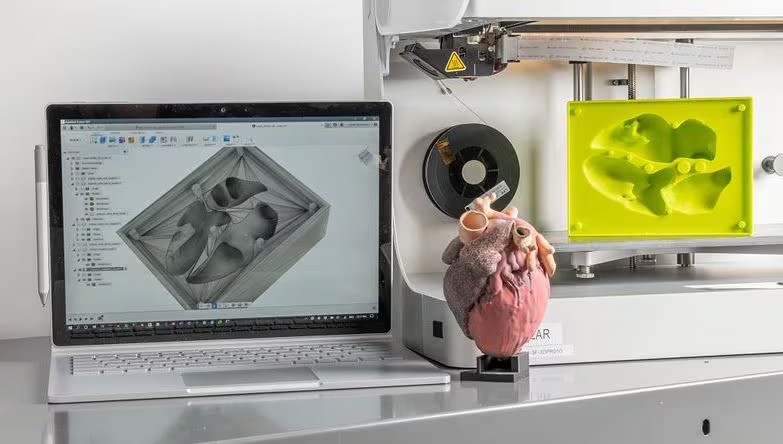
Rapid prototyping is essential for manufacturing various devices in the medical field, including surgical instruments, prosthetics, implants, and other equipment.
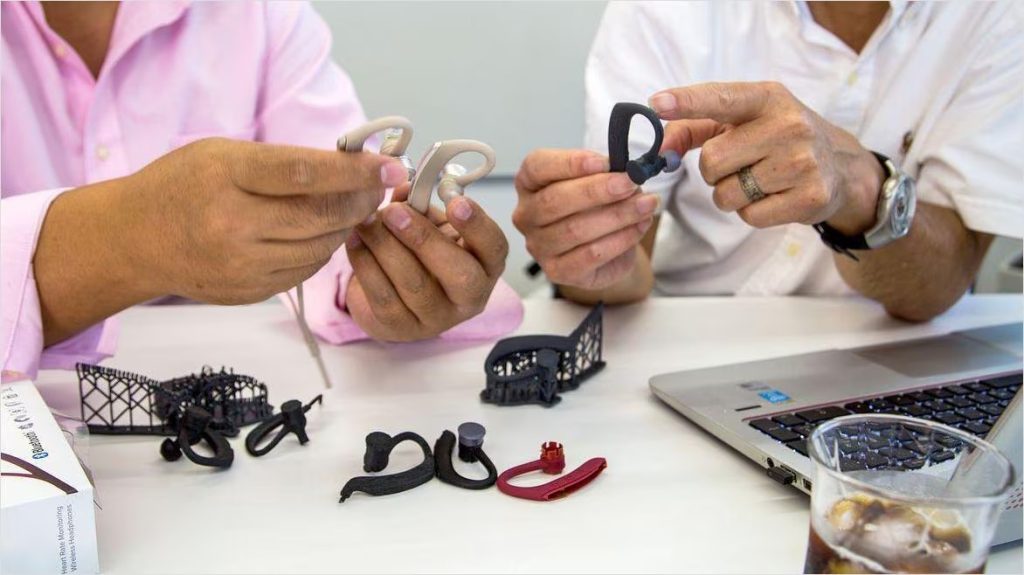
Types of rapid prototyping
Rapid prototyping is commonly linked with additive manufacturing methods, particularly 3D printing. Although there are other prototyping technologies available, most of them are too expensive to be considered as part of rapid prototyping. Take injection molding, for instance, its high costs and complex setup requirements make it impractical and costly for rapid prototyping purposes.CNC machining, which falls under subtractive manufacturing, can be a viable option for quickly prototyping parts that are not suitable for additive manufacturing. Nevertheless, the setup, operation, and tooling requirements for CNC machines are generally more time-consuming compared to 3D printers, resulting in their less frequent use for rapid prototyping purposes.
Consequently, rapid prototyping is often associated with numerous types of additive manufacturing. Fused filament fabrication (FFF), which is also referred to as fused deposition modeling (FDM) as a trademarked term, stereolithography (SLA), and selective laser sintering (SLS) are the three prevailing additive technologies.
FFF/FDM is widely regarded as the most favored method of 3D printing due to its user-friendly nature and cost-effectiveness. Additionally, it boasts a reasonably fast printing speed, making it particularly suitable for rapid prototyping purposes. Nevertheless, it is important to note that this technology’s process of depositing melted thermoplastics layer by layer may result in certain surface imperfections. Furthermore, it is worth mentioning that FFF/FDM exhibits the lowest resolution and accuracy among various 3D printing technologies, making it more suitable for the production of uncomplicated components and early-stage prototypes.
SLA and SLS 3D printing methods are pricier compared to FFF, but they offer superior results in terms of strength, functionality, and accuracy. SLA employs lasers to solidify a wide range of resins into durable plastic components with precise details and tight tolerances. This technique enables the rapid production of prototypes that closely resemble the final product in both appearance and functionality. On the other hand, SLS is a widely used approach for creating functional and engineering prototypes suitable for rigorous testing. By utilizing high-powered lasers, SLS fuses together particles from various powders, including metals, resulting in exceptionally robust parts that can incorporate intricate designs and unique characteristics.
Various 3D printing techniques used for rapid prototyping include selective laser melting (SLM), laminated object manufacturing (LOM), digital light processing (DLP), and binder jetting. SLM, also known as powder-bed fusion, is a metal additive method that constructs prototype or production parts layer by layer using titanium, aluminum, stainless steel, and other metal powders. DLP technology, similar to SLA, is quicker and more cost-effective, although it may necessitate support structures during printing and post-curing. LOM additive technology bonds layers of machine-cut paper, plastic, or other materials to create parts. Lastly, binder jetting is a rapid 3D-printing technique that can employ various material powders. It binds powder layers by spraying them with tiny liquid droplets, compacting the layers, and completing the objects with oven curing or sintering.
Benefits of rapid prototyping
Save time and money
In contrast to alternative approaches, the utilization of 3D printing for rapid prototyping enables significant time and cost savings by eliminating the need for complex machine setup and tooling.
Explore with freedom of concept
Due to the affordable price and minimal risk associated with developing quick prototypes, designers have the opportunity to examine their ideas in tangible form, resembling final products in appearance and texture.
Create with fast, iterative design
Utilizing 3D printing allows product teams to conduct additional design and testing iterations of rapid prototypes compared to conventional methods, all while maintaining a quick turnaround time in product development.
Communicate effectively
Physical models are more effective in communicating concepts and design objectives to clients and colleagues, enabling them to have a clearer understanding and provide valuable input for future design improvements.
Fix flaws early
Rapid prototyping enables designers and engineers to assess and test prototypes that resemble and function like final products at the beginning stages of product development, minimizing the chances of discovering design flaws later in the production process.
Customers using rapid prototyping
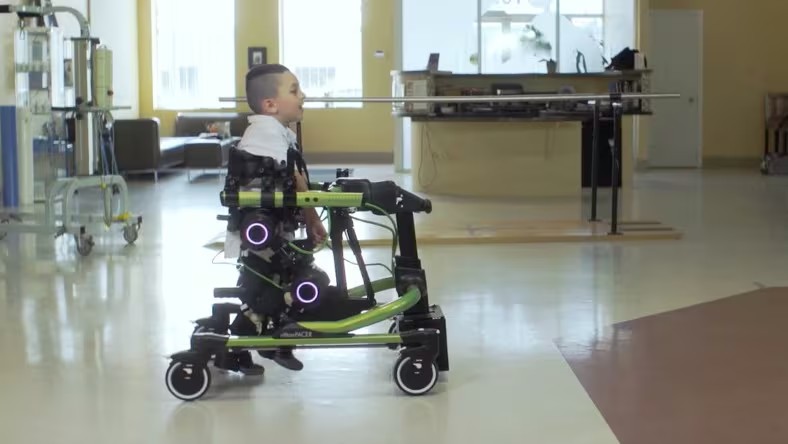
Robotics utilized rapid prototyping in the development of its wearable robotic device, which aids children with cerebral palsy in their mobility.
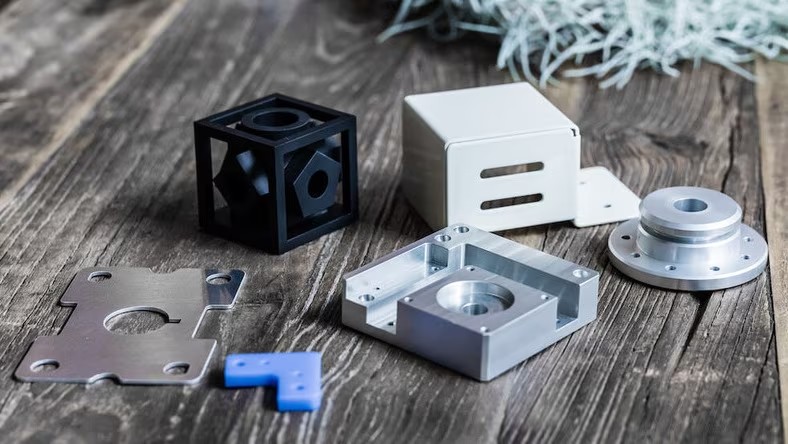
The AI-enhanced service provided by a Chinese manufacturer of machine parts offers swift prototyping and an astonishing range of parts in their catalog.
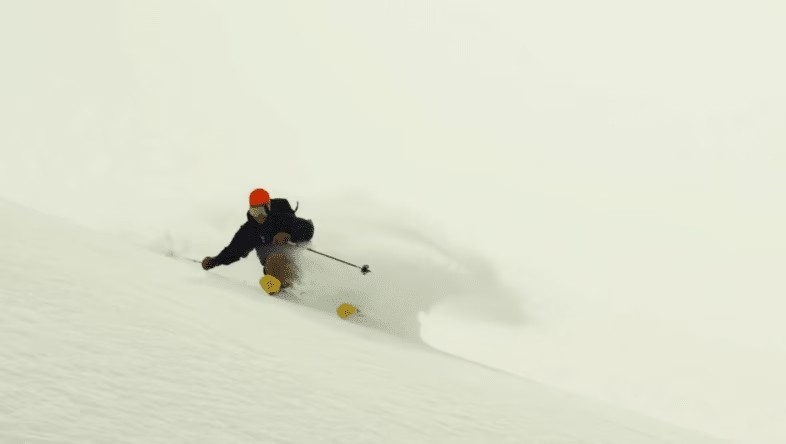
Our team conducted a study on biomaterials derived from microalgae and utilized rapid prototyping techniques to create a sustainable option to traditional petroleum-based skis.