X is not associated with high-speed milling, and it is not a recent innovation either. This technique has been employed in various industries, including mold manufacturing, for many years. Initially, it was considered a niche method for machines with high spindle speeds. However, high-speed milling has now expanded its scope and finds applications in diverse fields. Over the past few years, aluminum alloy has emerged as the predominant non-ferrous structural material in the industry, and the aluminum alloy sector has become a well-established market. When aluminum alloy is subjected to milling, what sort of sparks will be generated?
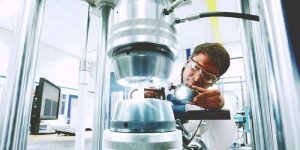
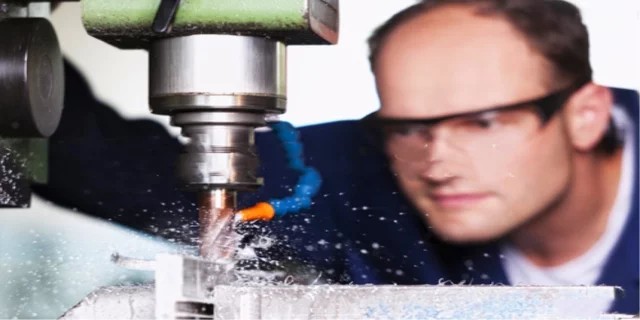
Development of high speed milling
1.Imagined version | high speed milling
During the 1990s, the emphasis in high speed milling (HSM) advancement was on the holistic approach, which involved designing machine tools with a spindle speed of 200,000 RPM. Both high spindle speed and high feed rate were considered crucial. Studies conducted by the research institute revealed that operating at high speeds could lead to severe repercussions and increased risks if the tool or machine part is not suitable for the specific application.
2.Optimize | milling application
The key elements to take into account include milling force, surface texture, metal removal rate, tool life, and safety. These investigations showcase the significance of enhancing factors related to high-speed milling. The wider application scope of high-speed milling is now possible thanks to the efforts of machine tool manufacturers, software developers, and milling tool manufacturers. What’s even more crucial is that high-speed milling has transitioned from being purely theoretical to being implemented across all areas of the workshop.
3.Innovate | milling tools
The mold manufacturing industry has greatly benefited from the advancement of innovative milling tools, as it has made high-speed milling a more practical and profitable method. The effectiveness of any milling process, including high-speed milling, relies on the quality of the machine tool, software, and milling cutter. Over the years, the development of high-speed milling tools has focused on enhancing performance. Milling plays a crucial role in the high-speed milling process, and its advancements directly impact the performance of milling cutters in various tool applications. Speed is of utmost importance in high-speed milling, encompassing spindle speed, milling speed, and feed. Achieving high-speed milling involves optimizing milling processes with increased milling speeds or feed rates.
New progress in aluminum processing
Blade fixation is of utmost importance when dealing with high-speed milling and indexable blades. The rise in spindle speed and table feed, particularly in aluminum milling, results in higher centrifugal force and subsequently, greater stress on the blade mounting components.
Finite element techniques are highly beneficial in the analysis of load distribution, aiding in the swift development of effective solutions and efficient models for indexable tools in high-speed milling. Furthermore, they can facilitate the creation of improved cooling systems. The incorporation of liquid channels and outlet structures ensures the optimal removal of chips. As a result, a new era of high-speed milling tools tailored for aluminum alloy milling has emerged.
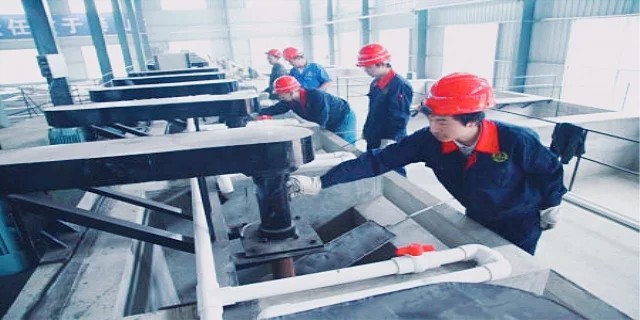
The CoroMill790 indexable end mill exemplifies a high-speed machining tool designed for aluminum alloys. Primarily utilized in mold manufacturing for cavity milling, edge milling, groove milling, profiling, and other high-speed processing techniques, this type of end mill secures the blade through a uniquely developed blade-knife interface. The serrated contact surface design between the bottom of the blade groove and the back of the blade enhances both the safety and precision of high-speed milling operations.The blade is evenly stressed, resulting in a smoother and safer processing experience, while also prolonging the tool’s service life. This design enhancement significantly enhances the milling quality and machining capacity.
The CoroMill790 end mill features a serrate contact surface design that is ideal for face milling cutters used in aluminum processing, particularly for cast aluminum parts like molds, engine blocks, and transmission housings. With the ability to handle semi-finishing to superfinishing, the milling speed can reach up to 8,000 m/min. The positive front angle of the CoroMill790 end mill can be crafted from cemented carbide, polycrystalline diamond (PCD), or cubic boron nitride (CBN), making it suitable for aluminum alloy and cast iron milling. Despite its high-tech structure, the CoroMill790 end mill is simple to adjust axially and offers benefits such as balanced milling force, wide application range, and precise machining allowance.
Additionally, every vehicle is equipped with four doors and two panels. The panels referred to are the engine panel and the trunk panel, both of which are susceptible to damage. The 5182 aluminum (AL 5182) utilized for the four doors and two panels is known for its exceptional ability to deform, allowing it to absorb impact and provide a high level of protection for the driver and passengers. To enhance safety measures, the doors and panels are constructed using 5182 aluminum alloy.
Furthermore, the car chassis is of utmost importance. Additionally, the suspension arm base plate of the vehicle is constructed using various types of aluminum alloy materials, including 5083, 5754, and 6061.
Furthermore, the aluminum alloy is utilized in the construction of the fuel tank, radiator, and battery floor of new energy vehicles.
Milling aluminum in automotive manufacturing
The utilization of aluminum alloy in automobile production is on the rise. Currently, the long wheelbase version of the Jaguar XF incorporates more aluminum alloy. This particular vehicle asserts that aside from the four exterior doors being constructed from steel, the remainder of the body is made from aluminum alloy, with the aluminum alloy proportion reaching 75%. Are you aware of which components of the car can be manufactured using aluminum?To begin with, let’s discuss the wheels. In the present day, car wheels are predominantly constructed using aluminum. If a car does not possess aluminum wheels, it is likely that it was manufactured over ten years ago or is simply a budget-friendly vehicle. The utilization of aluminum alloy wheels has a noticeable impact on diminishing the fuel consumption of automobiles, with the commonly employed alloy being 6061 aluminum (AL 6061) in the production of automobile wheels.
The possibilities for milling aluminum are endless
The advancement of the metal industry ensures that metal materials, from extraction to processing and disposal, are handled in a way that minimizes resource wastage and environmental harm. This makes aluminum alloy advantageous due to its eco-friendly nature, recyclability, and alignment with contemporary environmental concerns. The milling process expands the potential applications of aluminum in various aspects of our lives.