
EDM
- What is EDM and How Does it Work?
- Considerations in EDM
- Parts of a EDM Machine and EDM Selection
- EDM Process
- Differences Between EDM and Conventional EDM
- Top EDM Machine Manufacturers
- Applications, Advantages, and Disadvantages of EDM
What is EDM?
The process of precision machining known as electrical discharge machining (EDM) involves the removal of material from a workpiece using thermal energy instead of mechanical force. Wire electrical discharge machining (EDM), a type of EDM, utilizes a thin, single-strand metal wire and deionized water to conduct electricity, allowing for the cutting of metal without causing rust. In wire EDM, the tool electrode is typically a metallic wire made of brass or layered copper, which is used to cut or shape the workpiece. The thin electrode wire follows a specific path during the machining process. While electrode diameters can vary in size, they typically range from 0.004 inches to 0.012 inches (0.10mm to 0.30mm). The wire is coiled between two spools to ensure that the active part of the wire is constantly changing, preventing erosion that could lead to breakage.
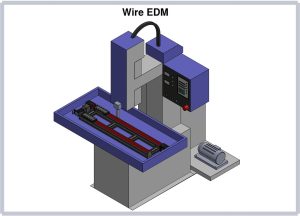
Wire EDM is a highly effective method for machining parts that are difficult to machine using traditional methods, provided that they are electrically conductive. Materials such as steel, titanium, super alloys, brass, and others that fall into this category can be easily machined using EDM. This process involves melting or vaporizing the material to create a precise cut line and produce small chips. EDM is widely used in various industries due to its adaptability, ability to cut strong metals, and its compact size. Wire EDM is particularly useful for accurately processing conductive and hard materials, allowing for the quick and precise cutting of complex structures with high tolerances. Additionally, it is a non-impact cutting technique, making it ideal for machining hard, brittle, and delicate materials without causing distortion.
How Does EDM Work?
During the wire EDM process, the material is cut, trimmed, and extracted from the workpiece. An electrical current discharge is created between the wire or electrode and the conductive workpiece. As the spark crosses the gap, material is eliminated from both the workpiece and the electrode. Wire EDM is particularly effective for machining hard conductive materials due to its unique characteristics. To prevent shorting out, a non-conductive fluid or dielectric is used. This dielectric also helps in removing the waste material, allowing the process to continue smoothly.
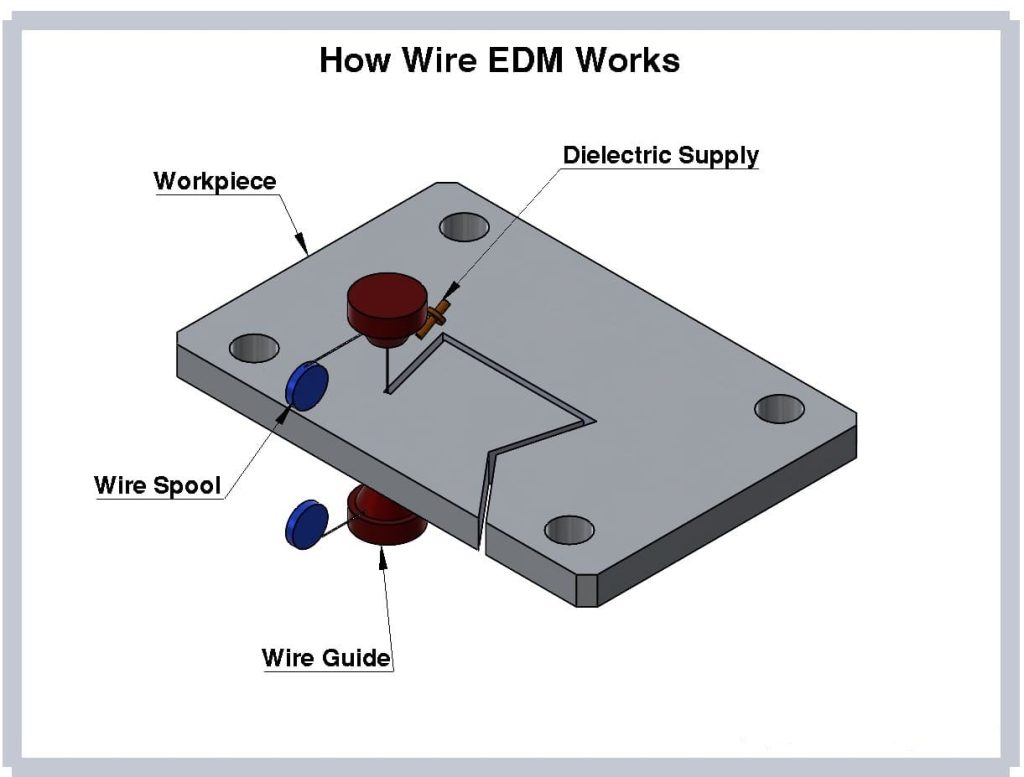
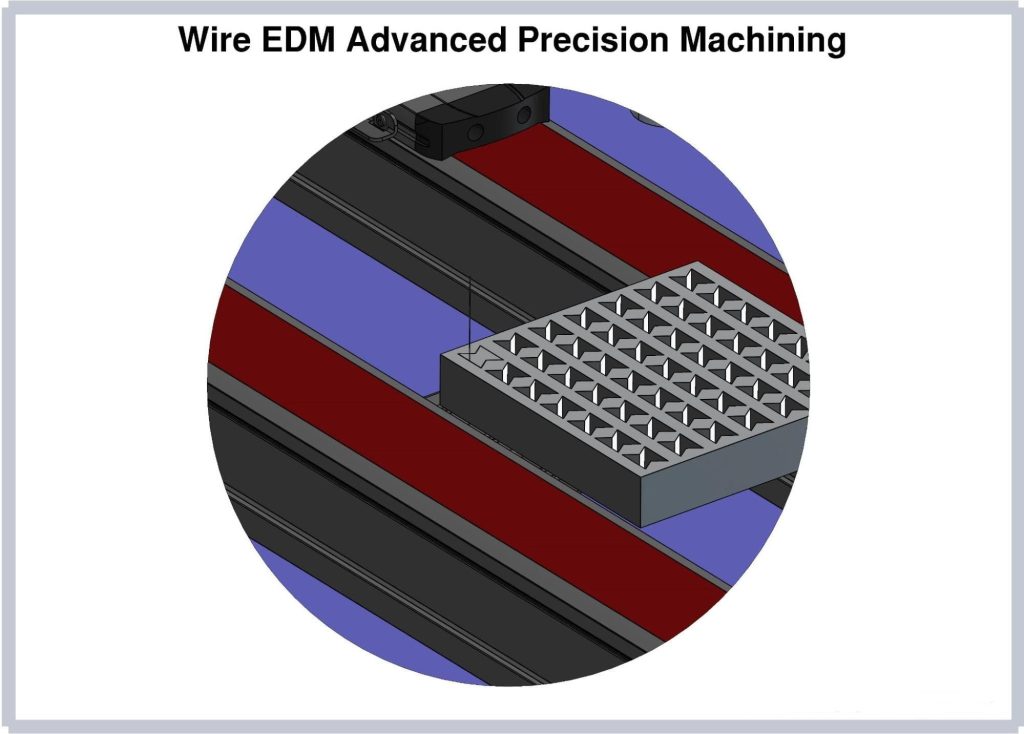
Before starting wire machining, it is necessary to create a hole in the workpiece or begin from the edge. Each discharge during the machining process leaves a crater on the workpiece and leaves a mark on the tool. The wire’s ability to be inclined allows for the creation of parts with taper or different profiles at the top and bottom. There is no mechanical contact between the electrode and the workpiece. Depending on the required accuracy and surface finish, a part may need to be cut, roughed, and skimmed. During a single cut, the wire should pass through a solid component before dropping a slug or scrap piece. While this design provides acceptable precision for certain tasks, skimming is often necessary. Wire EDM utilizes a potential difference that is pulsed onto the electrode and workpiece. This causes electrons from the negative electrode to flow towards the positive workpiece and collide with the deionized water molecules. The conversion of molecules into ions by the electrons increases the number of ions and electrons between the workpiece and the electrode. This process generates an electric current as the ions move towards the workpiece and the electrons move towards the electrode.
The electric current passing between the workpiece and the electrode causes the temperature to rise to nearly 10,000°C. The extreme heat melts and vaporizes the material farthest from the workpiece. Once the current ceases, the molten material is carried away by the dielectric fluid in motion. The accuracy of the wire EDM process is greatly influenced by the cutting parameters and speed. Higher speeds can cause the wire to slightly move or bend, leading to reduced overall accuracy. Therefore, maintaining lower power and speed levels ensures the utmost precision. Tolerances of up to +/- 0.0002 inches can be achieved with lower power and speed, while tolerances of +/- 0.001 inches are possible with higher speeds.
Types and Sizes of EDM Wire:The EDM wire’s diameter ranges from 0.0008 to 0.013 inches, with smaller wires necessitating lower power settings and slower cutting speeds. In over 80% of EDM work, a 0.010-inch diameter plain brass wire is employed. It is crucial to choose a wire that is appropriate for the material one intends to machine.
Part Geometry:Part geometry is a crucial consideration when determining the suitability of a design for wire EDM. It also plays a significant role in determining the level of difficulty in manufacturing the component. Initially, designers need to assess whether wire EDM can be utilized to produce the desired features. It is important to note that not all geometries are compatible with EDM and can potentially lead to problems such as wire erosion, variations in surface finishes due to material thickness, and limitations in achieving the desired tolerance levels. Therefore, engineers and designers should prioritize evaluating the geometry at the early stages of the design process to ensure manufacturability of the part.
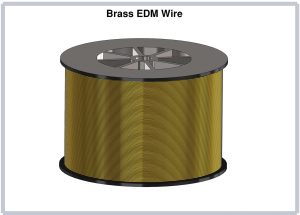
Surface Finish and Tolerance Requirements
When designing a product for wire EDM machining, it is crucial to carefully consider the requirements for the surface finish. Surface finishes achieved through wire EDM can reach an accuracy of up to 3 microinches. However, not all components need to be extremely precise. Only a small percentage of parts necessitate such a high level of accuracy and polish. Designers should take into account the minimum and maximum tolerance variations when engineering an object. Establishing minimal specifications will have a significant impact on the final product’s costs. Cost optimization, reduction of project lead time, and meeting the finished part’s repeatability requirements are all essential factors in the design process. For instance, the higher the surface polish in wire EDM, the tighter the tolerance. Nevertheless, this will result in increased costs as the part will require more cutting time overall. Moreover, the material type or part height can affect machining precision. Taller pieces will require more force to remove material, impacting precision and surface polish. Therefore, these factors must be carefully taken into consideration.
Material Thickness and Conductivity
The designer must inquire the client about the material selection when evaluating a project design. Additionally, the selection of the appropriate conductive material for wire EDM should be thoroughly examined. Opting for the right material that is conducive to wire EDM machining can lead to cost reduction in the final product, especially when material hardness, dimensional accuracy, and tight tolerances are necessary. It is crucial to assess and optimize each component of the part design to ensure optimal functional performance and minimize the overall product cost for an efficient wire EDM design.
Time Factor
Another crucial aspect to consider when designing a part for optimal manufacturability is the time factor in manufacturing. Given that EDM machining tends to be time-consuming, customer orders often demand a swift turnaround.
Working Table
The workpiece is held and supported by the work table, with two stepper motors controlling their motion. The wire EDM machining process is completed through the relative movement between the working table and cathode wire. The high-speed feed wire cut EDM machine’s work table features X and Y axis slides, utilizing a valuable linear guideway and ball screw for its movement components. The XY cross structure has a long history of use, establishing its mechanical rigidity and controllability, which are widely recognized. Presently, the production and design procedures for this technology are highly developed and commonly applied in various machine tools.
CNC Control
Precision stepper motors with robust coupling and detailed programming guidelines are vital elements within CNC systems. Furthermore, CNC tools oversee the complete wire EDM machining operation. Mastery of the entire process involves the capability to automate the cutting process and sequence the wire path effectively.
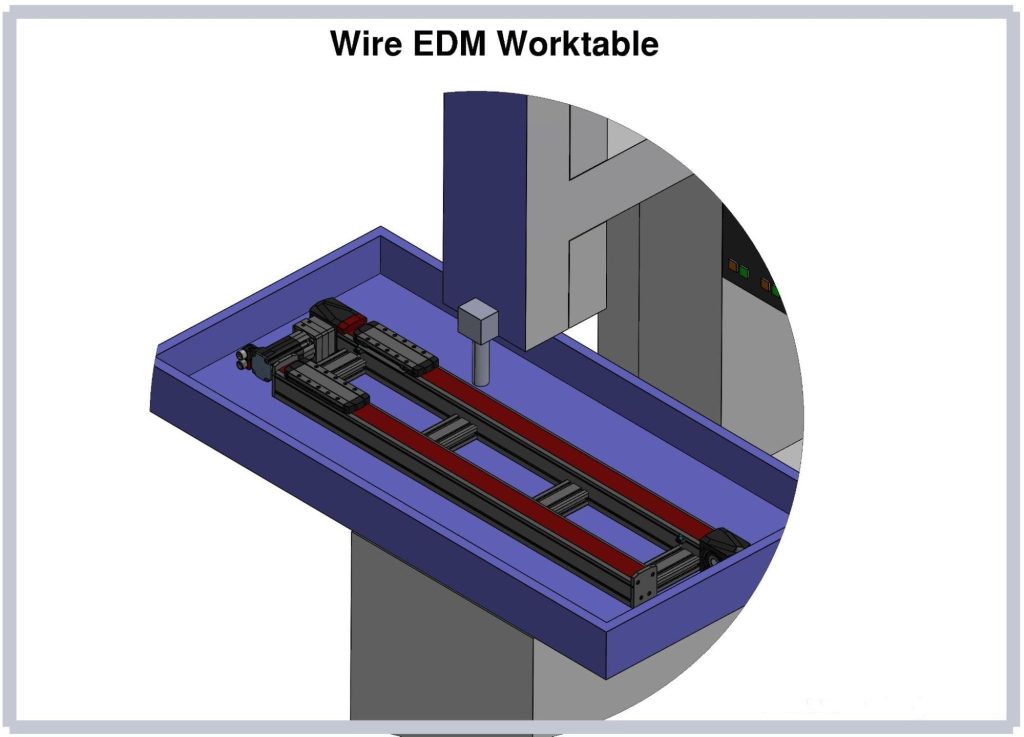
Wire Tensile Strength
It is of utmost importance to clearly define the tensile strength of EDM wire. The wire drive feed mechanism of the machine, consisting of a wire tensioner, roller guides, and upper and lower feed contacts, stretches the wire even if it does not make contact with the part during the cutting process (where the electric current is applied). The wire is preloaded with tension, which can be adjusted to carry out different cutting procedures. The ability of the wire to endure stress during cutting is determined by its tensile strength. The lower the tensile strength, the more susceptible it is to breaking.Angles can be cut in a wire with decreased tensile strength without fracturing. The U-V axis wire guides can be adjusted or shifted to produce significant tapers, and cuts at angles up to 45°. Utilizing the U-V axis to control the perpendicularity of vertical walls for accurate cutting, the more robust wire can be stretched with greater tension. Reducing wire tension during roughing enables the machine to cut at a faster rate without wire breakage. Slower speeds and reduced power are employed for skim cuts to attain optimal surface finish and precision.
Failure to Fracture:There is no definitive method for quantifying fracture resistance, hence it may be more precise to describe an EDM wire’s fracture resistance as wire toughness or resilience. This terminology is preferred due to the wire’s ability to endure the highly dynamic conditions within the spark gap.
Conductivity:Conductivity measures the ability of a substance to carry electrical current. If the wire used in EDM has higher conductivity, it allows for greater transmission of power to the workpiece. Improved conductivity often leads to higher cutting speeds, resulting in increased efficiency.
Temperature of Vaporization:A low wire melting temperature is ideal for achieving rapid vaporization. Instead of contaminating the gap with solidified chips, it is preferable for the wire surface to evaporate and quickly convert into gases.