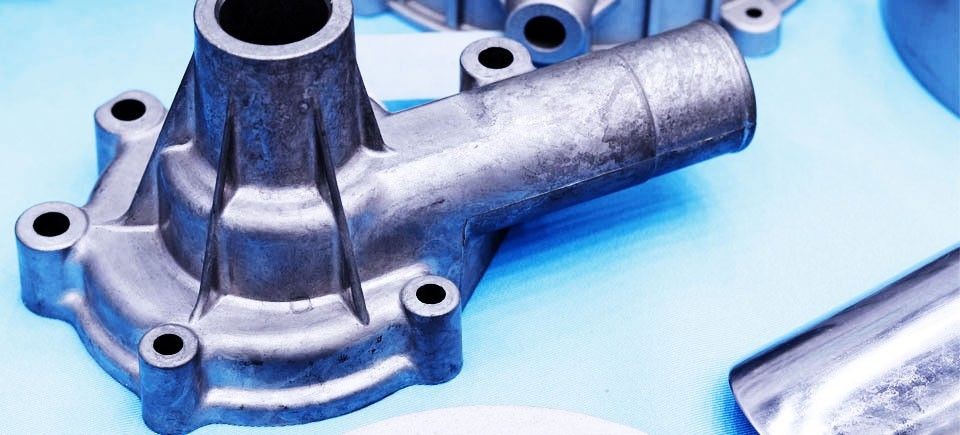
Zinc Alloy Die Casting
- Complete and cost-effective turnkey solution
- Quick lead time
- 20+ years of experience
Make MXY as Your Dependable Zinc Die Casting Provider
MXY boasts over two decades of expertise in delivering professional Zinc Die Casting services. Our zinc die-casting is sought after by customers worldwide for its top-notch quality and dependable performance. Rest assured, all our products meet international quality standards. Choose MXY for your Zinc Die Casting needs!
Full Range Solutions for Die Casting
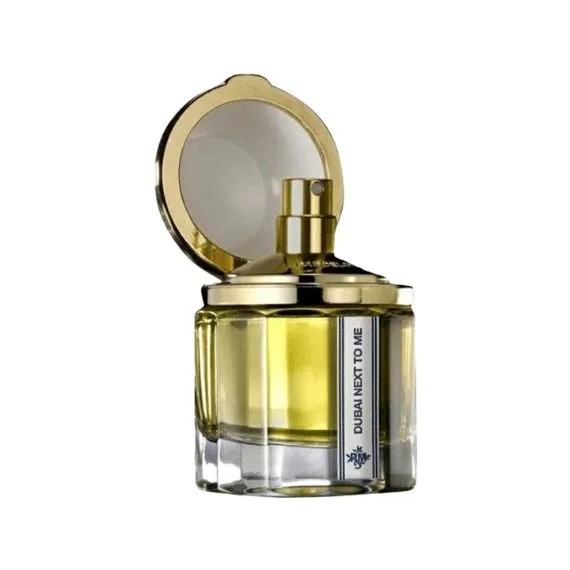
Our perfume bottle caps are manufactured using alloy. Product sizes can be custom-made based on your requirements.
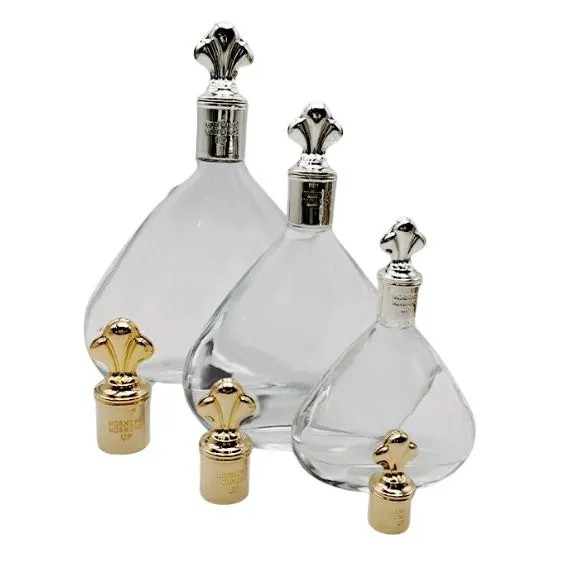
MXY creates zinc alloy bottle caps for spirits bottles and wine bottles with unique designs and well made outlook surface finishing.
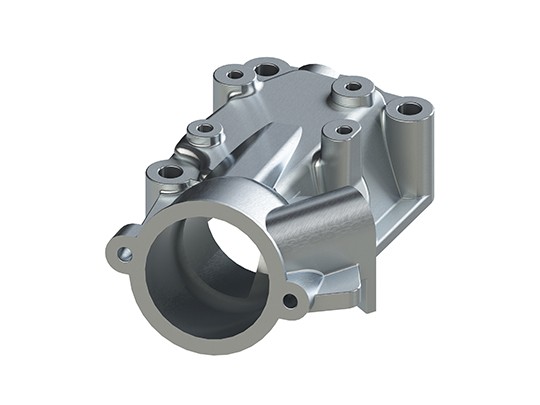
Zinc alloy die-casting accessories are produced using meticulously chosen materials, sleek finishes, and personalized characteristics.
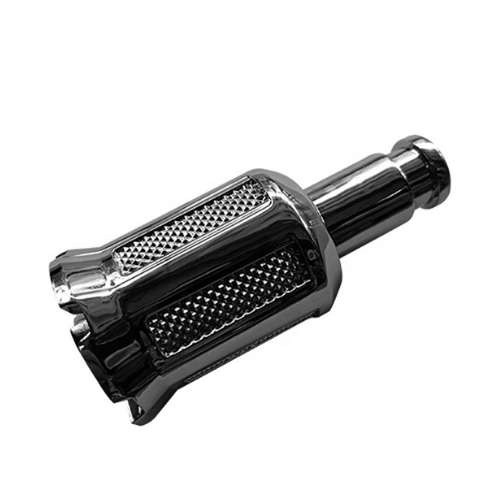
Our Zinc Alloy Artware Product Die Casting offers high machining accuracy, high strength, and a smooth surface finish.
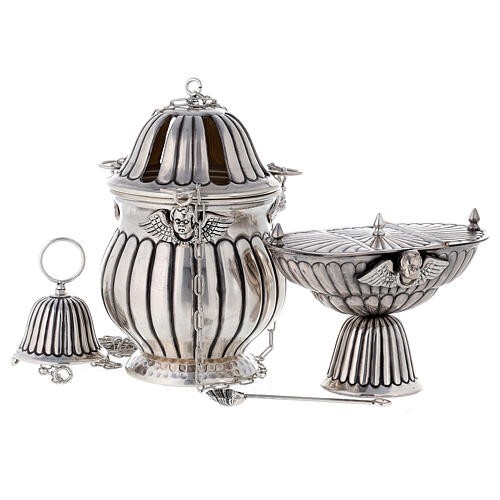
MXY offers Thurible Die Casting OEM, ODM service available in a various surface finish like e-coating, tin plating, etc.
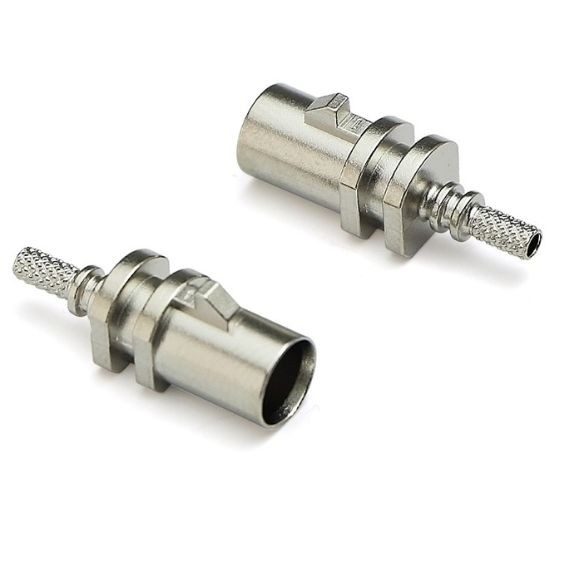
We offer a broad range of Zinc die casting tube for different industries applications, including connectors/terminals for battery management systems, etc.
Why Choose MXY Zinc Die Casting Parts
Fewer Failures
Die casting zinc alloy is more durable and exhibits greater fluidity when in its molten state compared to plastic or aluminum. It possesses superior impact resistance and robustness in comparison to its alternative materials.
Design Flexibility
Zinc alloys possess excellent flexibility, enabling them to shape and connect materials, thereby reducing the need for extra fasteners. This results in superior part designs suitable for various applications.
Eco-Friendly
Zinc, being completely recyclable, allows for the reformation and remelting of die casting techniques without any loss in quality. In comparison to aluminum, zinc alloys possess a significantly lower carbon footprint.
Better Finishes
We offer enhanced surface finishes for the required components. By employing plating or powder coating techniques, we can achieve decorative surfaces that possess both corrosion resistance and exceptional durability.
Zinc Die Casting Tooling Design
MXY boasts a team of more than 60 engineers dedicated to the development of in-house zinc die casting tooling. From the initial design phase to the production of final zinc die casting parts, our skilled engineers are here to support you every step of the way. Simply inform us of your zinc die casting requirements or send us your CAD drawing, and our MXY team will gladly assist you by conducting mold flow analysis to ensure optimal results.
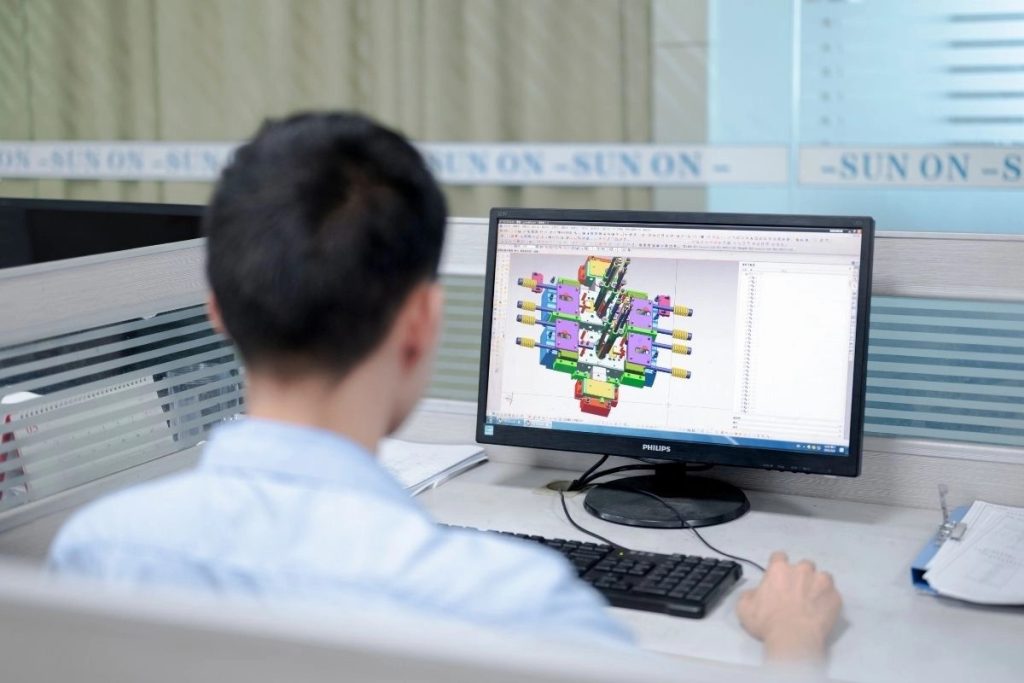
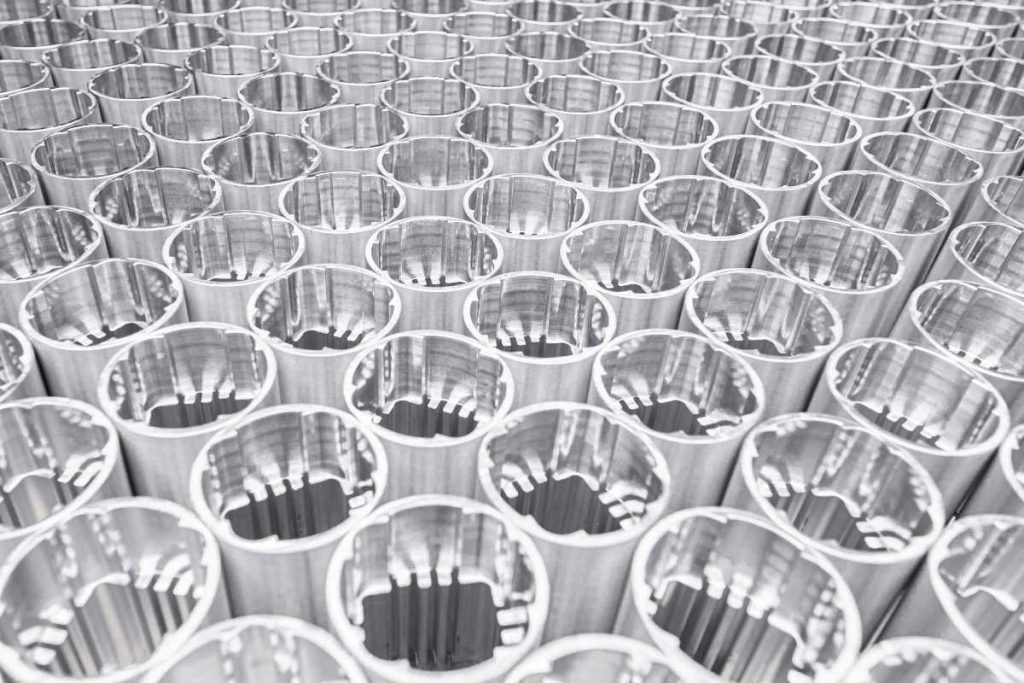
Zinc Alloy for Your Casting Parts
MXY frequently utilizes zinc alloys such as Zamac 3, Zamac 5, and Zamac 8 for the customization of zinc die casting components. However, we are open to using any alloy of your preference for your specific part. With over 20 years of experience in zinc die casting, MXY is well-equipped to assist you in selecting the ideal zinc alloy to create flawless zinc die casting parts tailored to your business needs.
Zinc Die Casting Techniques
MXY specializes in die-casting techniques, which are utilized to manufacture precise and necessary parts for specific applications. Two types of die casting methods are employed:
- Hot Chamber Die Casting: In this process, molten zinc is immersed inside a metal supporting furnace. The furnace is then connected to the machine through a feeding system or a gooseneck. This chamber is capable of producing approximately four to five shots per minute.
- Cold Chamber Die Casting: The molten zinc cast is poured into a cylindrical sleeve or cold chamber using a cold chamber die ladle. A hydraulically-operated plunger is employed to seal the port and apply pressure to the zinc, filling the die cavities.
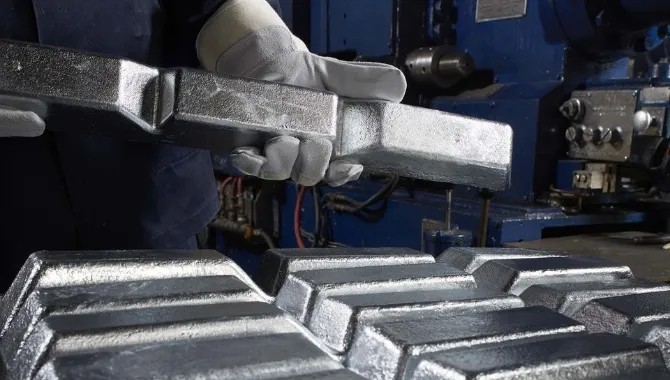
MXY – Your Trusted Zinc Die Casting Manufacturer

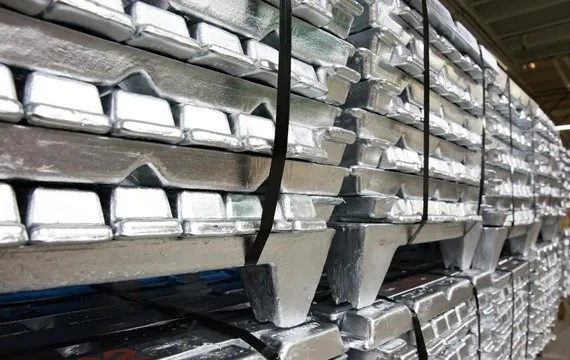
MXY is a reputable producer offering zinc die casting services and solutions. We specialize in manufacturing tailor-made components for a wide range of industrial uses, with a particular focus on the automotive sector. Through our zinc die-casting process, we transform raw materials into valuable products by applying heat and shaping techniques. Our company is equipped with state-of-the-art machinery, including both hot chamber and cold chamber machines, which are essential for efficient zinc die casting procedures. Moreover, our team of professionals diligently monitors every step of the production process using a cutting-edge real-time X-ray inspection machine. This meticulous approach ensures that we deliver high-quality, well-crafted, and satisfactory die-casted components.
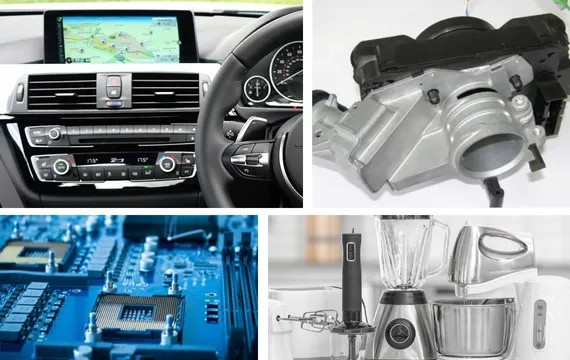
MXY manufactures die-casted zinc components, suitable for various industrial applications, such as follows.
- Electronics
- Automotive
- Appliances
- Cosmetic
- Architectural
- Construction
- Leisure sector
- Medical sector
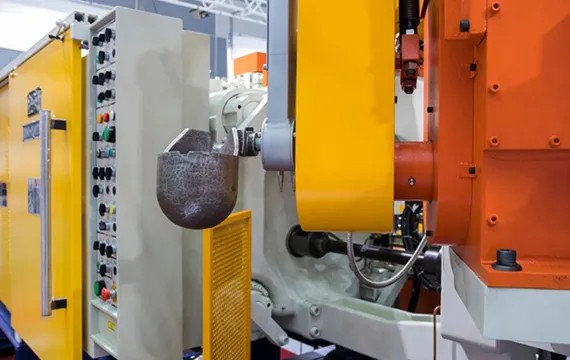
Die-casting zinc alloys offer several benefits. They result in robust parts due to their strength, allowing for thinner walls and less material usage. Additionally, zinc alloys enable the production of high-quality components with tighter tolerances, eliminating the need for costly machining. Moreover, the quick hardening of zinc alloys during die-casting enables fast production of numerous components in a short period. Lastly, the durability of zinc molds ensures a longer tool life compared to aluminum molds.
Zinc Die Casting Surface Treatment Options
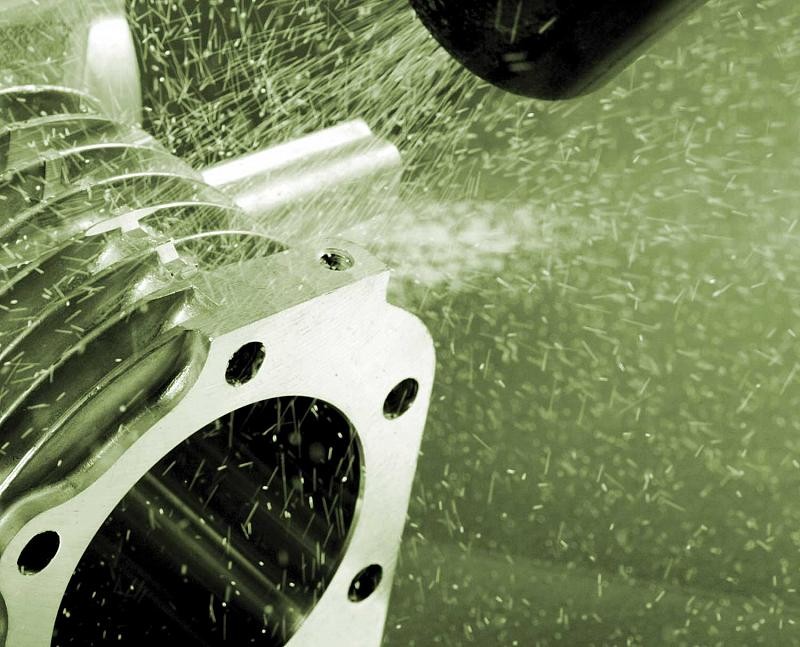
Sand Blasting
Sandblasting surface treatments are known for their ability to achieve a superior level of cleanliness and distinctive roughness. This not only enhances the mechanical properties of the workpiece but also provides resistance against fatigue. Moreover, this treatment significantly improves adhesion, prolongs durability, and adds to the aesthetic appeal of coatings. It is commonly employed in the electronics and appliances industry.
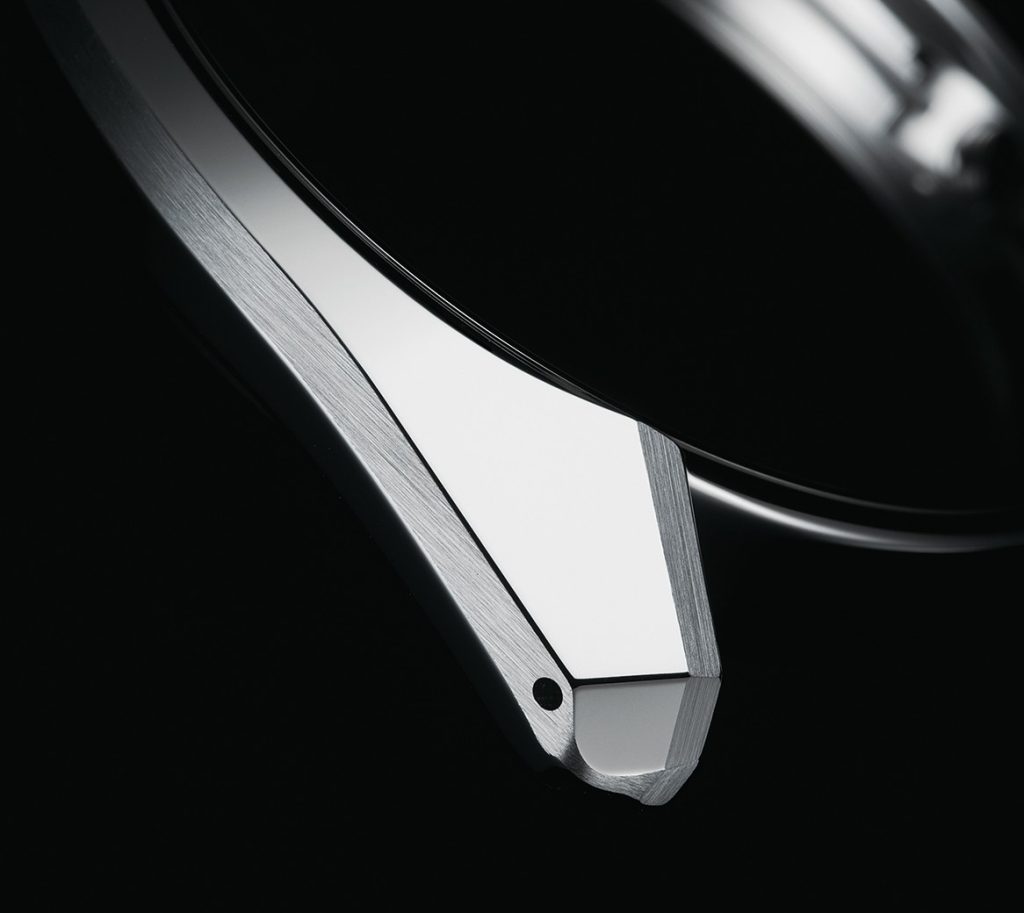
Polishing
The application of polishing treatments results in achieving smooth and lustrous surface finishes. These techniques can be categorized as chemical, electrolytic, or mechanical polishing methods. By employing these approaches, one can attain mirror-like effects, a sophisticated material appearance, and a trendy look for various components.
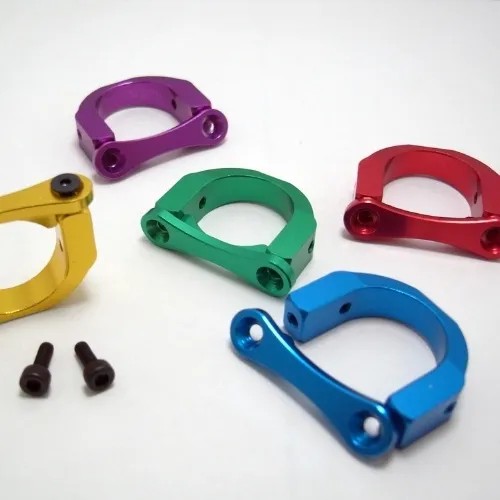
Anodizing
Anodizing treatments offer remedies for zinc surface wear resistance and hardness, ultimately prolonging the service life of zinc and enhancing its aesthetic appeal. This method of surface finishing is extensively utilized and has become an essential component of zinc alloy surface treatments.
Your One-Stop Zinc Die Casting Parts Provider
We are a reliable manufacturer of zinc die casting components that strictly follows ISO9001:2008 quality regulations. Our team of skilled engineers utilizes state-of-the-art die casting and CNC machines to guarantee the production of top-notch yet affordable parts. Feel free to reach out to us with your inquiries, and we will take care of the entire process.