The current manufacturing industry heavily relies on CNC machining parts due to their utmost importance. With the aid of computer numerical control (CNC), an advanced machining technology, precision cutting tools are controlled by computers to fabricate parts with intricate shapes effectively. These CNC machined parts serve as vital components in industries such as aerospace, automotive, medical devices, and electronics.
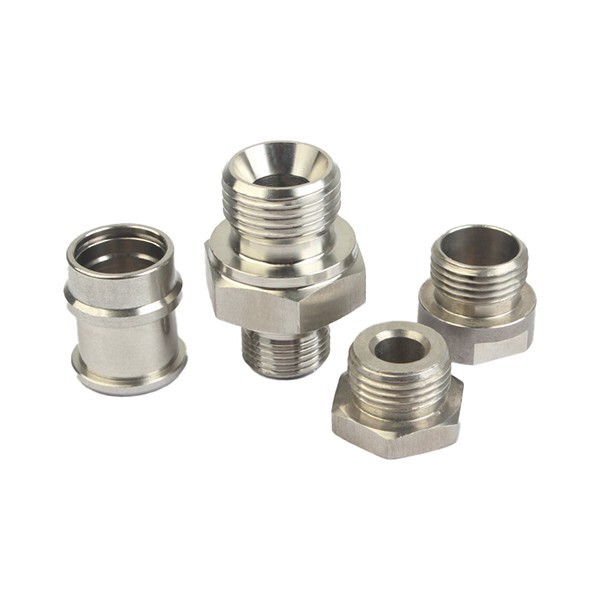
By harnessing the capabilities of pre-programmed software, CNC machining grants manufacturers the authority to manage the movement and functioning of the tool. This ensures that the results obtained are meticulously accurate and reliably uniform, eclipsing the possibilities of manual labor. Additionally, CNC machining possesses the versatility to work with an assortment of materials like aluminum, steel, copper, composites, and plastics. This adaptability facilitates the fabrication of workpieces that exhibit different levels of hardness and intricacy.
CNC machining parts offer a great advantage in terms of efficiency. Unlike traditional processing methods,cnc machining parts, it has the ability to greatly reduce the production cycle and minimize the need for manual intervention.As a result, there is a reduction in costs and a boost in production capacity. Additionally, CNC machining parts offer precise control, leading to lower scrap rates and guaranteeing that each part meets the necessary design specifications.
CNC machining parts find widespread use in industrial manufacturing across various applications. They are employed in crafting aircraft engine components, automotive brake parts, medical device sensors, and electronic device housings. The reason behind their popularity lies in their capability to produce intricate shapes with exceptional precision.
Technology is advancing rapidly, leading to higher levels of automation in CNC machining parts. This constant growth and evolution in CNC machining technology bring new opportunities and challenges to the manufacturing industry.Moving forward, as material science and software technology advance, CNC machined parts will remain crucial in pushing industrial manufacturing towards greater efficiency and sophistication.
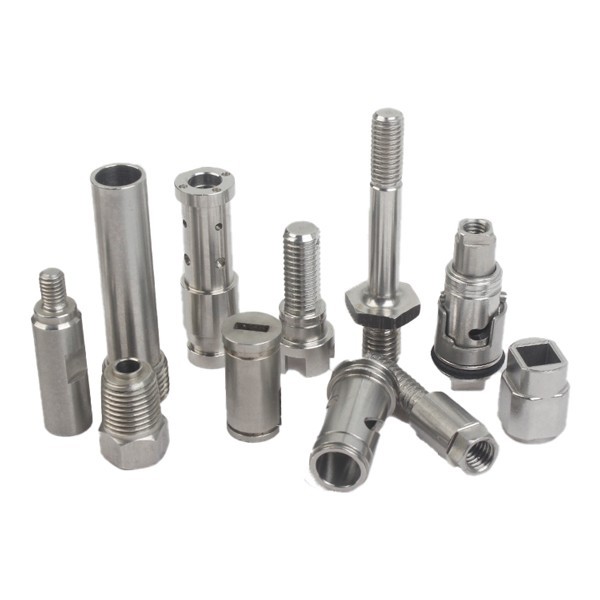
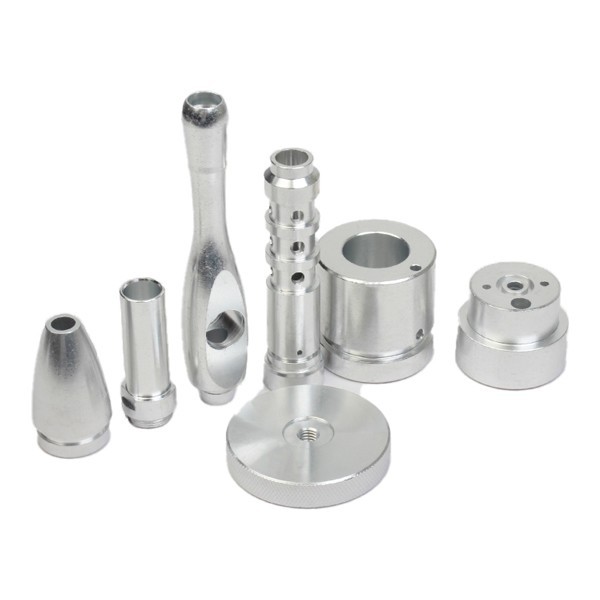
Factories can play multiple important roles in the field of CNC machined parts, which cover production efficiency, product quality, cost control and market competitiveness. Precision and complexity: CNC machining technology enables highly accurate and complex part manufacturing, more precise control of size and shape than traditional machining methods, and meet the high standards of design requirements. Production efficiency: Automated CNC systems can significantly increase production efficiency while reducing manual intervention. Factories can shorten production cycles by reducing equipment setup times and operating cycles, achieving faster delivery and the ability to respond to customer needs.
CNC equipment, despite its higher initial investment, can bring about significant cost savings in the long run. It achieves this by reducing scrap rates, cutting down on labor costs, and optimizing resource utilization. Additionally, the improved production efficiency allows factories to effectively manage their inventory and supply chain, leading to further cost reductions.
With CNC machining technology, flexibility and variety are at the forefront. It effortlessly accommodates a wide range of materials, including metals, plastics, and composites. Moreover, it can adeptly handle workpieces of different hardness levels and complexities. This adaptability empowers the plant to effectively meet the unique requirements of various industries and markets. By delivering tailor-made solutions, it enhances the competitiveness of the market.
By utilizing pre-programmed and automated control in CNC systems, the risk of human error is greatly minimized,cnc machining parts, guaranteeing that each part meets design specifications. This ultimately enhances the quality and reliability of the product.
To sum up, establishing a factory dedicated to CNC machining parts can greatly enhance production capacity, improve flexibility, elevate product quality, and reduce production expenses. This strategic move enables businesses to maintain a competitive edge in the market and fulfill customer expectations for exceptional customized products.
CNC machined parts are used in a wide range of industrial applications, including but not limited to:
Aerospace: Manufacture aircraft structural parts,cnc machining parts, engine parts, complex components of aerospace equipment, etc. Automotive industry: production of engine parts, braking systems, steering systems, transmission systems and other automotive parts. Medical equipment: Manufacturing precision medical equipment and instruments, such as surgical tools, prosthetics, implantable medical devices, etc. Electronic products: Processing components such as enclosures, radiators, connectors and brackets for electronic devices.
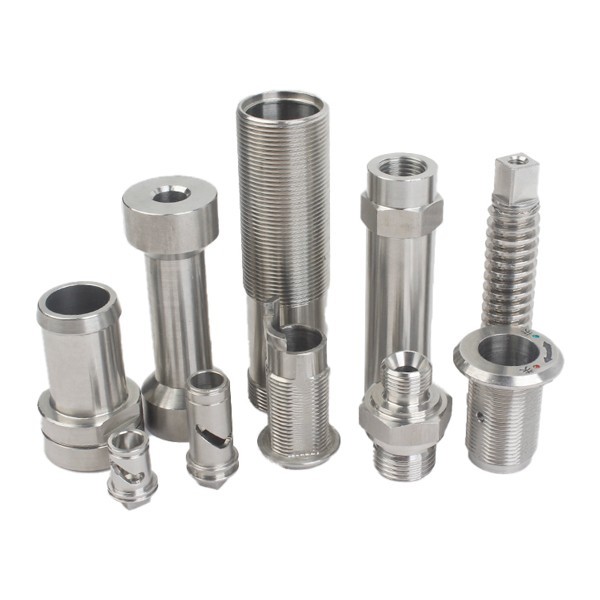
Energy industry: including components of power generation equipment, key components of energy conversion equipment. Military and Defense: Manufacture of various critical parts and components for weapon systems.
General manufacturing industry: including all kinds of mechanical equipment, tools, molds, fixtures, etc. Shipbuilding industry: production of ship hull structural parts, power system components, etc. Construction and building materials: Manufacture of components for building structures and construction equipment. Consumer goods manufacturing: including household appliances, toys, fashion accessories and other parts processing.
The manufacturing industry depends heavily on CNC machining technology to produce intricate and highly precise parts with exceptional accuracy, efficiency, and adaptability. With continuous technological advancements and its expanding applications, CNC machining is becoming indispensable in numerous fields, driving growth and fostering innovation.