Table of Contents
What are the main restrictions of CNC design?
CNC provides excellent design flexibility, although there are some constraints to consider. These limitations are associated with the fundamental mechanics of the cutting process, particularly focusing on tool geometry and tool accessibility.
Tool geometry
Most CNC cutting tools, like end mill tools and drills, generally have a cylindrical shape with a limited cutting length.pp polypropylene cnc machining service As the tool is used to machine a workpiece, its shape is transferred onto the material, creating machined components with precise geometries.cnc metal machining powder coating Consequently, even when utilizing small cutting tools, internal corners of CNC parts will always exhibit a certain radius.
Tool access
When removing material, the cutting tool approaches the workpiece directly from above. Features that are inaccessible in this manner cannot be CNC machined.
There is one exception to this guideline: undercuts. More information on undercuts can be found towards the conclusion of this article.
We suggest aligning all features of your model (such as holes, cavities, vertical walls, etc.) to one of the six principal directions. However, consider this as a suggestion rather than a limitation, as 5-axis CNC systems provide advanced workpiece-holding capabilities.
Tool access becomes a concern when machining features with a significant depth-to-width ratio. For instance, to access the bottom of a deep cavity, tools with extended reach are necessary. This requires a broader range of motion for the end effector, leading to increased machine chatter and reduced achievable accuracy.
Simplifying production can be achieved by designing parts that can be CNC machined using a tool with the largest possible diameter and the shortest possible length.
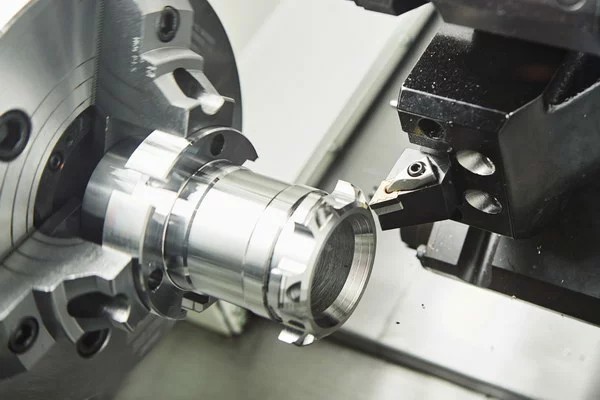
essential design techniques
CNC machining design
In this extensive guide to CNC machining design, we have compiled essential design techniques and advanced suggestions to help you achieve the best possible results for your customized components.cnc machining centre.There are a number of straightforward measures that can be employed to improve the effectiveness of your computer numerical control (CNC) machining designs.suzhou cnc machining By adhering to design-for-manufacturing (DFM) principles, you can make the most of the vast capabilities offered by CNC machining.cnc machining 5axis Nevertheless, this can prove to be quite difficult as there is a lack of universally acknowledged industry standards.
optimal design techniques
This article provides a comprehensive guide on the optimal design techniques for CNC machining.cnc machining bike parts To compile this comprehensive and current information, we sought input from professionals in the industry and CNC machining service providers. If your aim is to reduce expenses, make sure to consult this manual on developing economical components for CNC.cnc machining service china
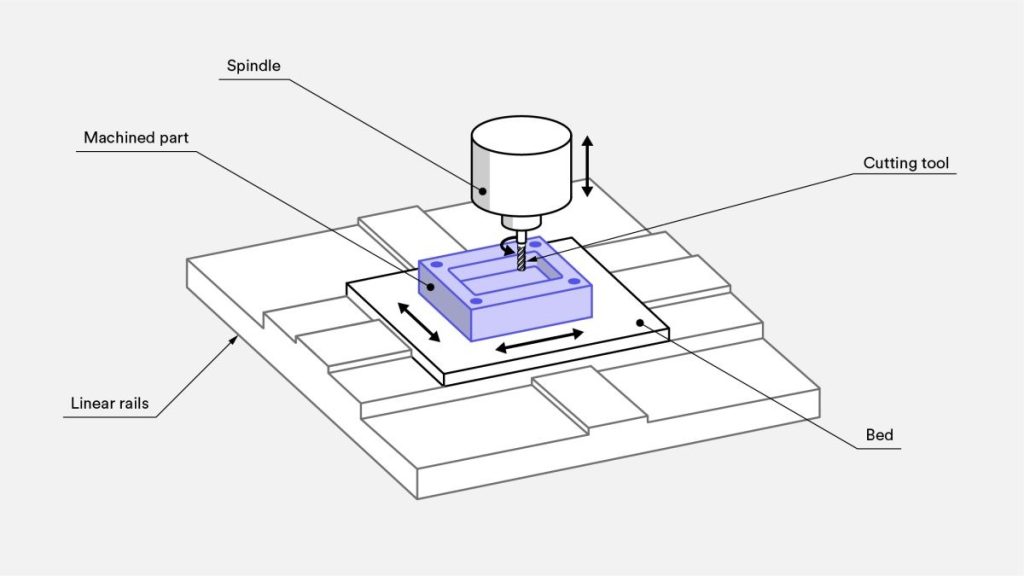
how the CNC machining process works?
CAD models
CNC machining is a manufacturing process that involves the removal of material from a solid block to create parts.brass cnc machining services This is achieved by using cutting tools that rotate at high speeds based on CAD models.cnc machining parts 4140 The process is suitable for working with both metals and plastics.cnc 4 axis machining CNC-machined parts are recognized for their accurate dimensions and close tolerances, making them ideal for mass production and custom projects.cnc machining turning part It is worth noting that CNC machining is considered the most cost-effective method for producing metal prototypes, outperforming 3D printing in terms of efficiency.cnc machining aluminum dropshipping Delve into our comprehensive guide on the core concepts of CNC machining.cnc vertical machining center price
CNC design guidelines
specific standards
One common obstacle encountered during the design of a part for CNC machining is the absence of industry-wide specific standards. The capabilities of CNC machines and tools are constantly being enhanced by manufacturers, pushing the boundaries of what can be achieved. The following table provides a summary of suggested and achievable values for the typical features found in CNC machined parts.
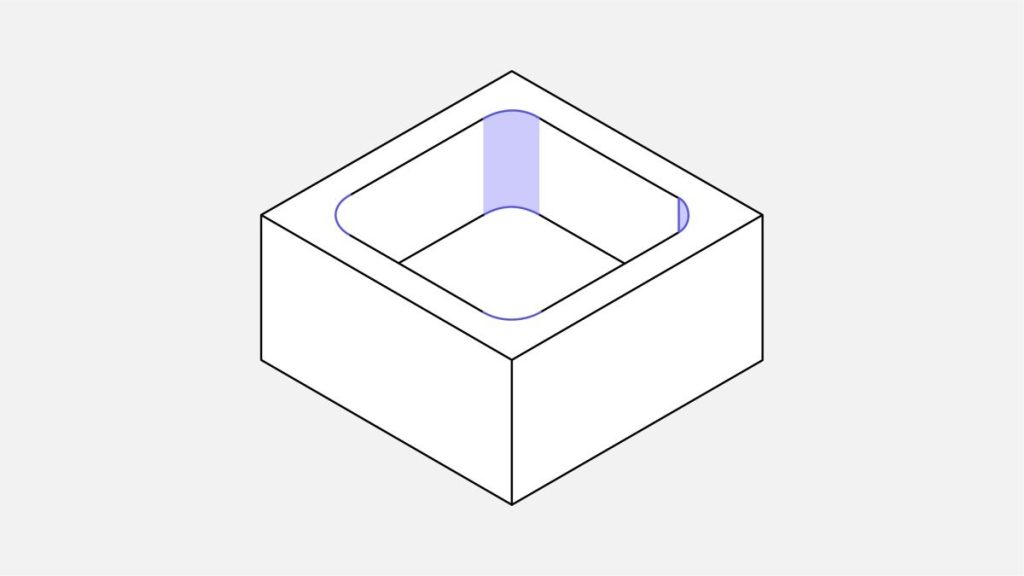
cavity depth
Recommended cavity depth: 4 times the width of the cavity.
End mill tools have a restricted cutting length, typically around three to four times their diameter. When the depth-to-width ratio of cavities is smaller, issues such as tool deflection, chip evacuation, and vibrations become more prominent.
To ensure satisfactory outcomes, it is advisable to limit the depth of the cavity to four times its width.
If deeper depths are necessary, it may be worth considering the design of parts with a variable cavity depth.
For deep cavity milling, cavities with depths exceeding six times the tool diameter are classified as deep. Specialized tooling allows for a tool diameter-to-cavity depth ratio of up to 30:1, with a maximum depth of 35 cm achievable using a 1-inch diameter end mill tool.