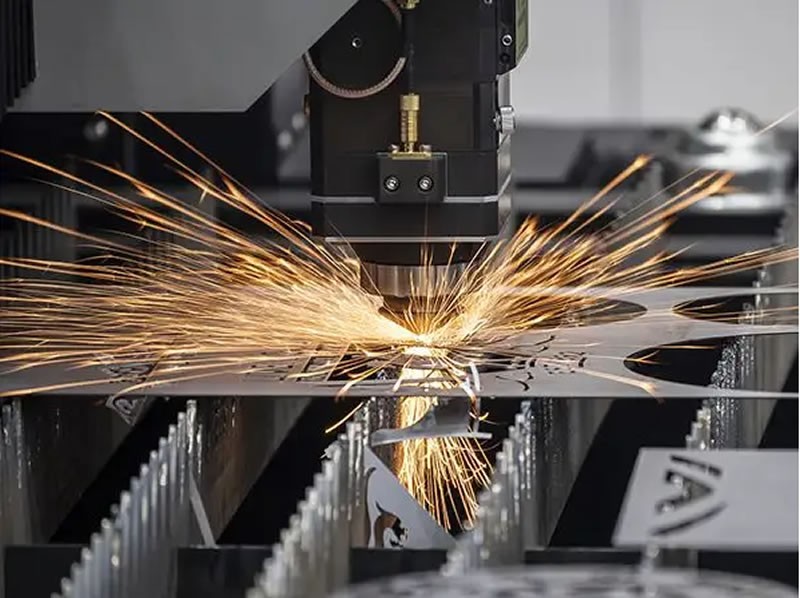
Magnesium alloy, with a specific gravity of only 1.8, is the lightest metal structure material. It surpasses aluminum by 2/3 and iron by 1/4 in terms of weight. Despite its lightweight nature, it boasts a remarkable strength of 133, comparable to aluminum. Additionally, it exhibits exceptional properties such as strong resistance to shock, electromagnetic interference, high thermal conductivity, and electrical conductivity. Moreover, it is an environmentally friendly material as it can be fully recycled without causing pollution.Magnesium alloy, being the lightest metal material, along with its high specific strength, excellent vibration dissipation, and superior ability to withstand impact loads compared to aluminum alloy, offers substantial weight reduction advantages and notable enhancement in the combat performance of aircraft. It is commonly employed in various aircraft components such as landing gear, hatches, reinforcements, engine parts, propellers, and structural elements.
Electronic products and transportation, along with other industries that rely on lightweight materials, have a significant impact. The utilization of magnesium alloy in 3C electronic products provides various benefits, including reduced weight, a sleek and shiny look, vibrant colors, and the ability to meet individual preferences.Additionally, the recyclability of magnesium alloy aligns with the current societal focus on environmental protection. Currently, magnesium alloy is not only utilized in the production of notebook computers, Walkmans, and digital cameras, but also in military computers, communication devices like cell phones, televisions, plasma displays, hard disk drives, advanced audio-visual equipment, LED lighting, and other equipment.
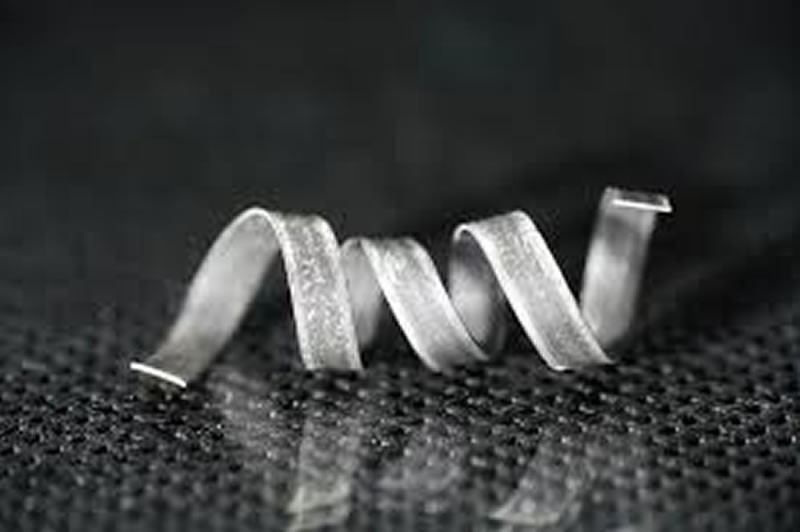
Magnesium alloy’s exceptional biocompatibility and degradability have positioned it as a central focus of research in the medical field, attracting increasing interest from researchers globally. Magnesium, a prevalent trace element in the human body, is essential for various metabolic processes. Its impressive mechanical properties closely resemble the elastic modulus of human bone, reducing the risk of adverse reactions between implants and bone elasticity, thus promoting bone tissue healing. Furthermore, its biodegradability eliminates the need for painful and mentally stressful secondary surgical removal of the magnesium alloy.
Where does magnesium & magnesium alloy come from?
Nature is abundant with magnesium, making it one of the most prevalent elements. It proudly claims the eighth spot as one of the Earth’s crust’s most abundant elements, contributing approximately 2% to its overall mass. Moreover, it secures the ninth position as one of the universe’s most abundant elements. When it comes to smelting magnesium, there are two primary methods: the electrolytic method and the silicon heat method.
The thermal reduction of magnesium oxide produced from carbonate ore by calcination can be achieved with the use of ferrosilicon. This particular method is commonly referred to as the Lijiang method. The Lijiang method is a widely employed technique for the production of magnesium metal. Different raw materials like dolomite ore, fluorite, silica ore, coke, and waste iron are used in the process. Dolomite ore undergoes calcination in a rotary kiln to produce albite. Albite is then crushed, along with separately crushed fluorite.The mixture of albite and fluorite is then combined in a mixing ball. On the other hand, the silica ore, coke, and scrap iron are introduced into an electric arc furnace for a reaction. The resulting mixture is crushed to obtain ferrosilicon powder. This ferrosilicon powder is then added to the mixture in the mixer and fed into a ball making machine. The resulting mixture is subsequently placed into a reduction furnace, along with pellets containing ferrosilicon and fluorite.
You can get magnesium chloride solution from spinel, brine, or seawater by dehydrating or baking magnesium chloride melt, then using electrolysis. This process, called the electrolysis method, includes breaking down molten anhydrous magnesium chloride into magnesium metal and chlorine gas at high temperatures. The electrolysis method is considered a highly promising technique for magnesium refining due to its advanced production process and low energy consumption. In developed nations, the electrolysis method is widely employed to produce more than eighty percent of magnesium metal. To form magnesium alloys, additional elements are mixed with the purified magnesium metal, resulting in various shapes such as plates, billets, rods, tubes, sheets, bars, and wires. These alloys are carefully molded and sized before being sent to other companies or manufacturers for further processing into a wide range of products.
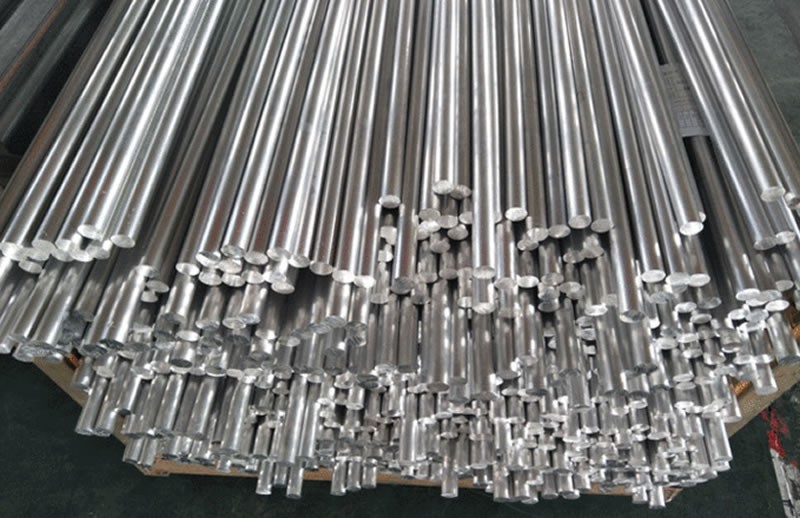
What kinds of magnesium alloy can be divided into?
As it is widely acknowledged, magnesium alloy is primarily composed of magnesium metal. By incorporating various other elements and forming an alloy, magnesium alloy includes alloy elements such as AL, Zn, Mn, Si, x, Cu, Li, and certain rare earth group elements. The classification of magnesium alloy can be based on its alloy composition as well as the processing methods and performance utilized. Hence, magnesium alloys can be categorized into the following three groups.
1.Based on the categorization of magnesium alloy composition.
Magnesium alloys are classified based on their chemical composition, which includes five main alloy elements: manganese (Mn), aluminum (Al), zinc (Zn), zirconium (Zr), and rare earth elements. The types of alloys include Mg-Mn, Mg-AL-Mn, Mg-Al-Zn-Mn, Mg-Zr, Mg-Zn-Zr, Mg-Re-Zr, Mg-Ag-Re-Zr, and Mg-Y-Re-Zr.
2.According to the classification method for processing magnesium alloys.
There are three main categories of magnesium alloy based on processing methods: casting, deformation, and hot dip plating. Casting and deformation alloys are commonly used, each with distinct composition and metallurgical organization performance. Casting magnesium alloy is primarily utilized for die-casting transportation equipment, machinery, electrical and electronic products, and other spare parts. It offers high casting efficiency, excellent surface quality, fine and uniform grain, and the ability to produce thin wall thickness and complex shapes. On the other hand, deformation magnesium alloy is mainly used for forging and extrusion, providing high strength performance and excellent plasticity.
3.Based on the classification of magnesium alloy, taking into account its performance and utilization.
Magnesium alloy is classified based on its performance and usage, which includes creep-resistant, mold, wear-resistant, anti-corrosion, and structural types.
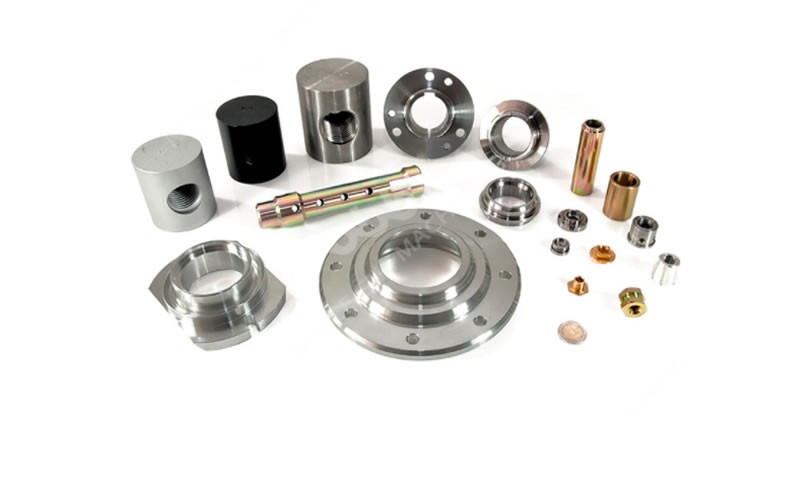
What is CNC machining?
CNC machining, also referred to as Numerical Control Machining, is a method utilized to fabricate parts on a CNC machine tool. Although the procedures for CNC machine tool machining and traditional machine tool machining are mostly alike, there have been notable differences as well. This method involves controlling the displacement of parts and tools using digital information. The main goal is to efficiently address the issues presented by different components, small production runs, and intricate shapes, all while maintaining accuracy and achieving streamlined and automated operations. The machine tool’s controlled functions involve initiating and halting the machine tool, starting and stopping the spindle, altering the rotation speed and direction, managing the feed motion in terms of speed, direction, and technique, choosing the appropriate tool, adjusting for length and radius, swapping out tools, and activating and deactivating the coolant system, among other tasks.
What types of magnesium alloys are used in CNC machining?
Magnesium alloy can be divided into two categories based on the molding process: cast magnesium alloy and deformed magnesium alloy. These two types have distinct differences in terms of their composition and structural characteristics.
1. Casting magnesium alloy CNC machining.
The process of magnesium alloy casting involves blending magnesium with alloying elements to produce a suitable magnesium alloy for casting parts. Casting magnesium alloy is the most commonly utilized magnesium alloy for casting. Various methods such as sand chain making, metal casting, extrusion casting, and fusion casting can be employed for casting magnesium alloy. This type of alloy is mainly used in manufacturing automotive parts, machine parts, shell covers, electrical components, and other products. Die-casting is the favored production technique for casting magnesium alloy due to its high efficiency, precise outcomes, and top-notch castings.
2. Deformed magnesium alloy CNC machining.
Magnesium alloys that have been through deformation processes exhibit enhanced mechanical properties and structural integrity when compared to cast magnesium alloys. Deformation aids in minimizing structural defects, leading to increased strength, improved ductility, and a wide range of mechanical properties suitable for different engineering structural components. The primary techniques for deforming magnesium alloys consist of extrusion, rolling, and forging. Deformed magnesium alloys are extensively utilized in CNC machining due to their machinability, superior surface quality, and decreased wear on cutting tools.
What are the common CNC machining processes for magnesium alloy?
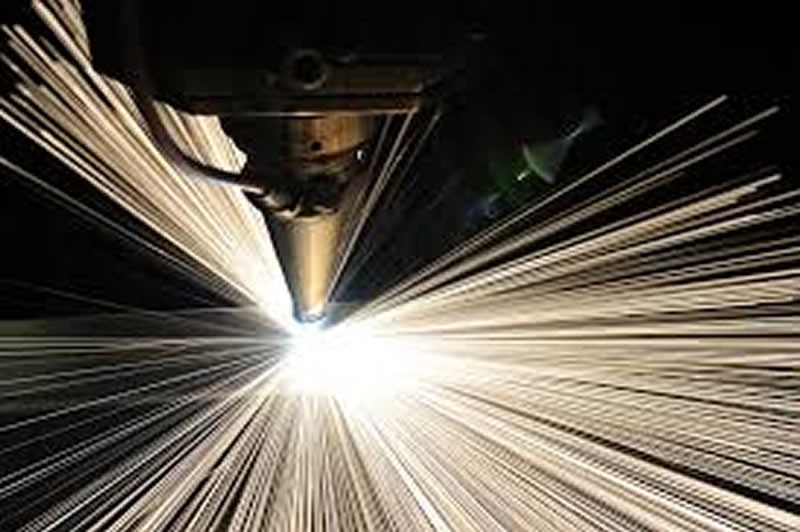
1.The extensive use of CNC milling machines in machining magnesium alloy parts is attributed to their versatility and efficiency. These machines employ a rotary cutting tool to accurately remove material from a stationary block of magnesium alloy. With CNC milling machines, you can effortlessly machine flat surfaces, internal and external contours, holes, threads, and more on various parts. The flat contours are typically machined using two-axis linkage, while the spatial surfaces are machined using two-and-a-half, three-axis, or multi-axis linkage. Due to the movement characteristics of the machine tool, a CNC milling machine can also function as a CNC drilling machine or CNC boring machine, allowing for complete milling, boring, drilling, reaming, tapping threads, and other processes.
2. Laser cutting magnesium alloy CNC machining.
The CNC laser cutting machine utilizes a laser beam to illuminate the surface of the metal plate, resulting in the release of energy that melts the plate and enables the gas to remove the resulting slag. The cutting table holds the metal plate in a horizontal position, while the computer controls the path of the powerful laser beam. Laser cutting machines are known for their energy efficiency and precision, surpassing plasma cutting machines in these aspects, thus making them ideal for cutting thin sheets. However, it is worth noting that only the most robust and costly laser cutting machines are capable of cutting through thick or dense materials.
3, water-cutting magnesium alloy CNC machining.
The waterjet, also known as a CNC water cutting machine, uses powerful water jets to accurately cut different materials by passing through a small nozzle. Thanks to computer control, it can intricately carve the workpiece without being affected much by the material’s texture.Water cutting is considered a cold cutting method, as it involves the addition of abrasives during the metal cutting process to achieve desired results. This technique does not involve any chemical reactions, thermal deformations, or alterations to the physical and chemical properties of the material being cut.