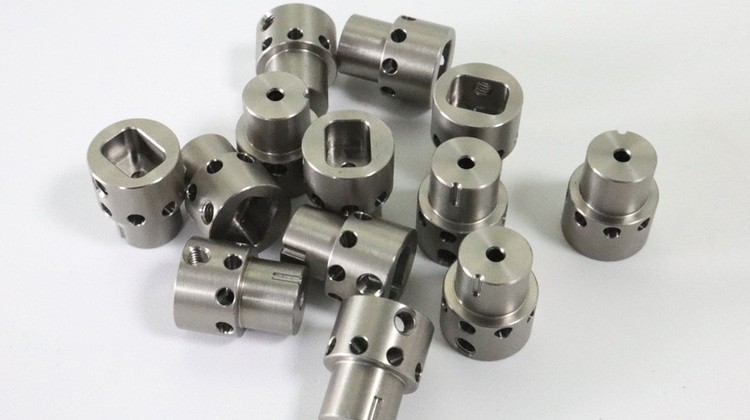
Stainless steel CNC machining introduction
Stainless steel CNC machining is responsible for revolutionizing manufacturing procedures across industries, presenting unmatched precision and efficiency. Success stories can be told within various industry segments where this advanced technology, leveraging computer-controlled machinery, is embraced for meticulously shaping stainless steel parts to precise measurements. Industries, such as aerospace, medical devices, automotive sectors, and consumer electronics, attribute much of their success in producing high-quality and resilient parts to CNC machining.
Precision engineering
Stainless steel is recognized for its ability to resist corrosion and its strength, yet it encounters specific difficulties during processing because of its tough and hard nature. CNC machining is able to tackle these challenges by keeping precise tolerances and creating intricate shapes. CAD software aids in meticulous planning, allowing engineers to enhance designs for easier manufacturing.
Process overview
The exceptional corrosion resistance and strength of stainless steel are well-known, but its hardness and toughness present unique obstacles during processing. CNC machining effectively overcomes these challenges by maintaining tight tolerances and crafting complex geometries. CAD software plays a crucial role in precise planning, empowering engineers to optimize designs for manufacturability.
Advantages of CNC machining stainless steel CNC machines are capable of achieving accuracy down to the micron level, guaranteeing that parts consistently meet exact specifications.CNC machining is flexible enough to meet a wide range of production requirements, from creating prototypes to mass production.Automated systems help decrease mistakes made by humans, boost productivity, cut down on waste, and make the most out of materials.CNC machines are capable of handling intricate shapes and features that would pose a challenge for traditional machining methods.

Apply
CNC machining of stainless steel has a wide range of applications: Aerospace: Critical components such as turbine blades and structural components. Medical: Surgical instruments and implants that require biocompatibility and precision. Automotive: engine parts, brackets and special accessories. Consumer electronics: enclosures, connectors, and internal components of electronic devices.
Conclusion
Stainless steel CNC machining is instrumental in fostering innovation and setting high standards in manufacturing. Thanks to the continuous advancements in CNC technology, products are not only meeting industry requirements but also exceeding expectations in terms of reliability and longevity. CNC machining stands as a cornerstone in precision engineering, offering a seamless integration of quality and effectiveness.
In short, the combination of CNC machining and stainless steel opens up endless possibilities, pushing the boundaries of what modern manufacturing can achieve. The factory plays a vital role in CNC machining stainless, which is reflected in the following aspects:
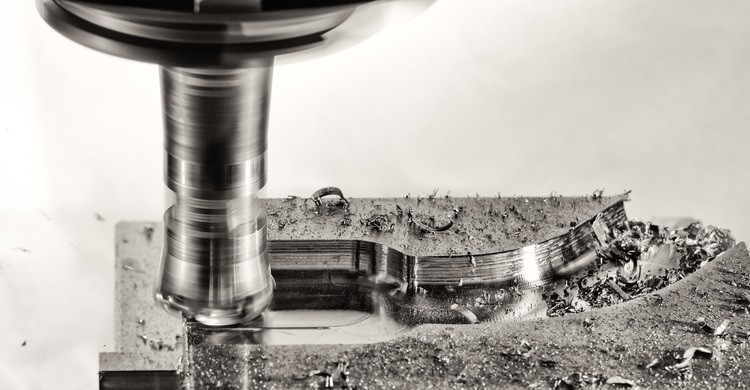
Technical expertise and equipment investment The plant’s technical expertise and investment in equipment are fundamental to achieving high quality CNC machining stainless. The modern factory ensures that it has the most advanced CNC machining equipment and precision tools through continuous technological updates and equipment upgrades. These investments not only improve production efficiency, but also ensure the control of product quality and precision.
Process optimization and cost controlBy optimizing processes, factories can make the most out of CNC machining advantages, like precise cutting parameter control, tool path optimization, and selecting the right machining strategies. This not only boosts processing efficiency but also helps in managing production costs effectively, leading to economic benefits through waste reduction and minimizing manual adjustments.
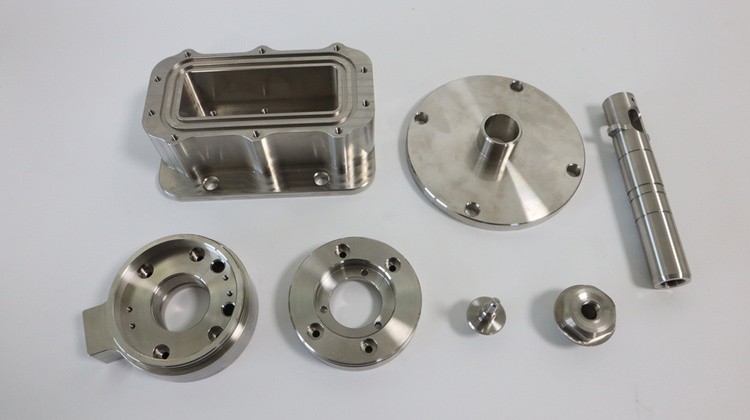
Quality assurance and reliable delivery The factory plays a key role in ensuring product quality in CNC machining stainless.Strict quality control processes and inspection standards ensure that every part meets design requirements and customer expectations. This quality assurance not only enhances the reliability of the product, but also establishes the basis for long-term cooperation to provide customers with a stable supply.
Innovation and customer demand response The factory can adapt quickly to customer demands thanks to its innovative approach and adaptable production capabilities. This involves creating prototypes, tailoring solutions, and enhancing engineering for particular needs. Collaboration with customers allows for the development of new products and a strong market advantage.
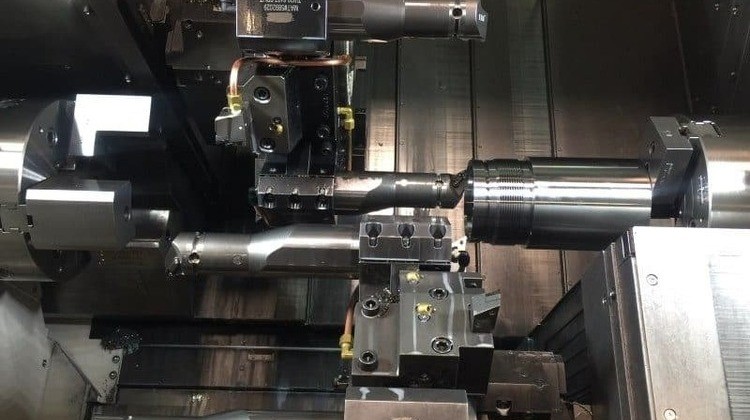
Environmental and social responsibility Contemporary factories are increasingly focusing on environmental and social responsibility. They are cutting down on resource consumption and environmental impact by utilizing energy-efficient and eco-friendly processing technologies and sustainable production practices. This sustainable business concept not only meets industry standards and regulations but also boosts the corporate image and market competitiveness.
Typically, the factory’s role in CNC machining stainless steel goes beyond simply producing machining parts. It involves leveraging technical expertise, optimizing processes, ensuring quality assurance, and fostering innovation to deliver customers with top-notch and efficient processing services. This, in turn, drives industry growth and bolsters market competitiveness.