Sheet metal fabrication is a skilled practice that involves transforming flat metal sheets into finished products through cutting and shaping techniques. This method is widely used in various industries, including robotics, automotive, aerospace, medical, construction, and electronics. Common materials like steel, aluminum, copper, and brass are preferred in sheet metal fabrication, catering to different metal thicknesses. Cutting, bending, punching, and welding are integral steps in this process, necessitating tools like shears, lasers, plasma cutters, press brakes, rollers, and stamping machines.
What is Sheet Metal Fabrication?
Creating Sheet Metal Parts: A Step-by-Step Guide
Working with sheet metal fabrication can be quite intricate, making it difficult for people to fully grasp the process. Unclear specifications often result in unrealistic expectations and requests for the project. Additionally, choosing the right raw materials for machining is a complex task, as it is essential to select the material that can best achieve the desired shape. The production of metal parts involves a series of steps that must be followed from start to finish.
Designing Engineering Blueprints.
The initial stage of sheet metal fabrication is all about design and engineering. This important phase requires the use of computer-aided design (CAD) software to develop intricate drawings or 3D models of the product. The design takes into consideration various factors like dimensions, tolerances, material choices, and the specific needs for the final application.
Developing a prototype version.
To maintain the form of the component after creating a sheet metal design model, engineers employ various techniques such as welding, cutting, bending, punching, and stamping. Surface treatments are also used to enhance the aesthetics of the final prototype. Following a specific order when carrying out these procedures is vital. Skipping a step or rushing through the process may impact the integrity and quality of the end product.
Analysis of manufacturability is crucial in the production process.
After receiving the drawing, the engineer will carefully inspect it to ensure that it meets all the necessary requirements and specifications. By utilizing DfM strategies, an engineering analysis is conducted, offering valuable insights to engineers in order to create designs that are easily manufacturable. Once the analysis of manufacturability is completed, detailed shop drawings are generated, which include calculations of stress/strain levels and load capacities. The information provided in these drawings will determine the procedure for sheet metal fabrication. Finally, a DFM report is prepared for the customer’s review.
Testing the prototype.
Customers will evaluate the prototype to make sure it fits their needs. It might also involve testing in actual environments. Additionally, taking into account users’ input on the products could be part of the evaluation process.
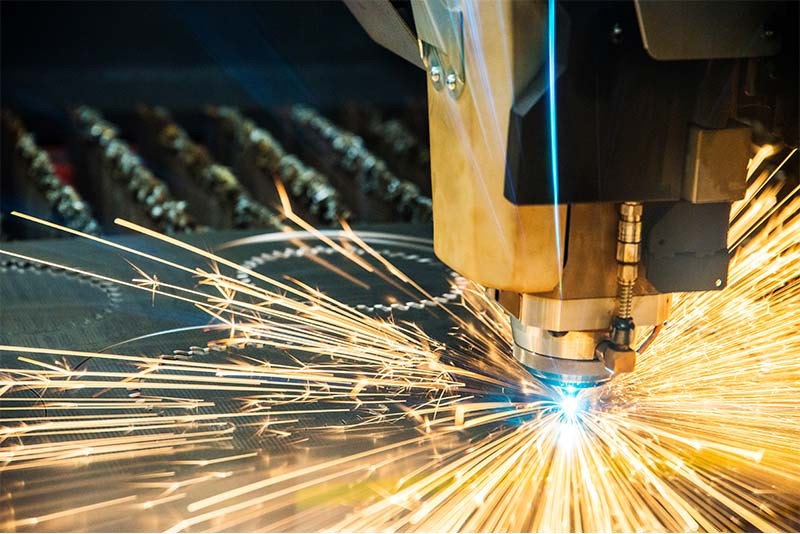
Sheet metal fabrication involves the process of shaping and forming metal sheets to create various products.
The process of sheet metal fabrication begins with extracting materials from a thin sheet metal stock placed on a flatbed. Then, cutting tools are used to follow pre-programmed part patterns and create the desired shapes. Different subtractive machining technologies can be used for this task. Depending on the part’s geometry, additional features like internal holes and edge features can be generated using a sheet metal punch, shear, laser, waterjet, or plasma. After cutting, the pieces are sent to the press brake for material deformation, such as bending, to achieve the final geometries. Finally, the sheet metal pieces are either assembled together or combined with non-sheet metal components to form a finished product. Surface finishing operations are often applied in many cases.
From Sheet Metal Prototyping to Manufacturing.
Sheet metal fabrication is flexible, whether you’re starting with a prototype or moving on to mass production. Transitioning from prototyping to full-scale manufacturing demands careful planning, accurate manufacturing methods, and strict quality control measures to ensure consistent and reliable production of sheet metal components.
Rapid Tooling
Tooling or molds are created quickly and accurately using fast methods like 3D printing, CNC machining, or laser cutting. These techniques ensure efficient production of tooling. Rapid tooling in sheet metal fabrication leads to faster production turnaround times while maintaining precision and quality standards. This is particularly beneficial for small to medium production runs or situations that call for rapid prototyping and design improvements. Utilizing rapid tooling methods enables manufacturers to accelerate the sheet metal fabrication process, reduce costs, and enhance the overall production process.
Rapid Prototyping
Rapid prototyping is a widely used method in sheet metal fabrication to quickly create prototypes of sheet metal components for design verification and validation. Specialized fast prototyping techniques tailored for sheet metal are employed in this process, accelerating the validation of design concepts and saving time and costs compared to traditional methods.
Batch Production
n the realm of sheet metal fabrication, batch production entails the sequential manufacturing of a specific quantity of sheet metal components. The process encompasses design and planning, material preparation, tool setup, and production runs. By employing various fabrication techniques such as cutting, bending, welding, and finishing, the sheet metal is shaped, trimmed, and assembled. Batch production offers several advantages, including enhanced efficiency, cost-effectiveness, and consistent quality,
Common Types of Sheet Metal Fabrication Processes
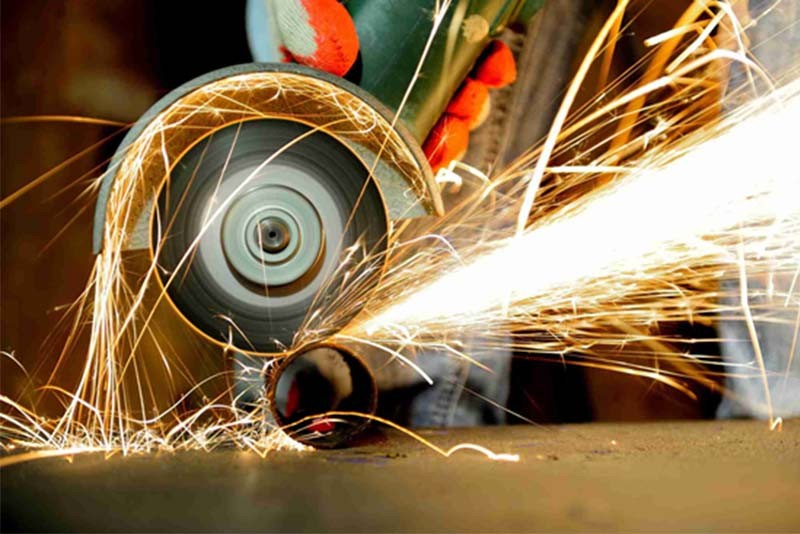
Sheet Metal Cutting
Cutting sheet metal is a crucial step in the process of shaping and sizing sheet metal. It involves removing material to achieve the desired dimensions and shape. When choosing a cutting method for a sheet metal project, it’s important to consider precision, metal thickness, and the complexity of the design.
Laser Cutting
Opting for laser cutting is opting for an extremely accurate and efficient way to cut sheet metal. By using a powerful laser beam, it can melt and vaporize the metal along a designated path. Laser cutting is highly favored in sheet metal fabrication for its ability to generate precise cuts with smooth edges and minimal distortion.
Plasma Cutting
A plasma torch is utilized in plasma cutting to slice through a variety of metals effectively, providing fast and accurate cuts on different materials and thicknesses. It can effortlessly cut through steel, aluminum, stainless steel, copper, brass, and titanium. Despite its speed and efficiency, thinner materials may lead to rough edges and less precise cuts.
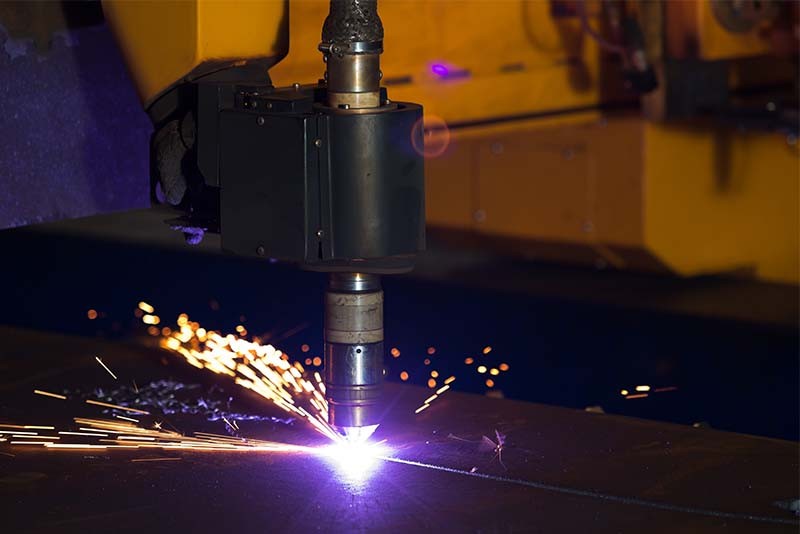
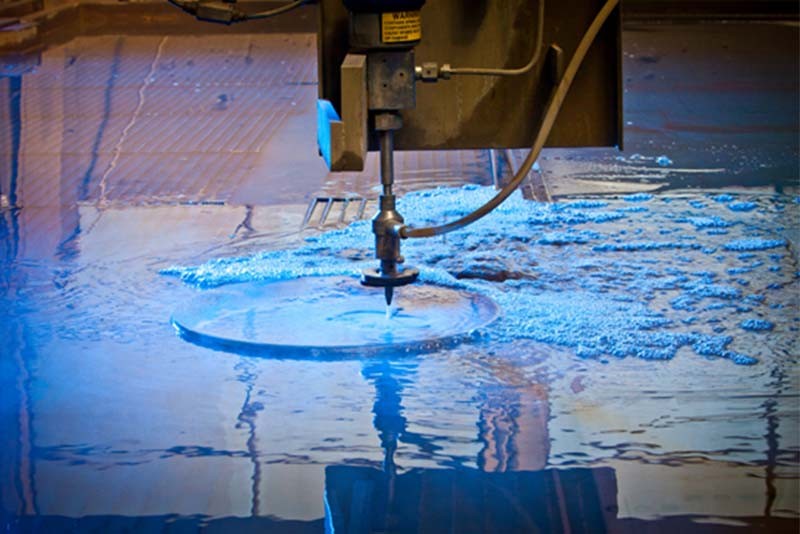
Waterjet Cutting
Waterjet cutting involves using a high-pressure water stream mixed with abrasive particles to cut through metal efficiently. This technique is widely used in sheet metal fabrication because it can create precise cuts in different materials and thicknesses. One benefit of waterjet cutting is its ability to produce accurate cuts with minimal distortion. It is suitable for cutting metals, plastics, and composites. Despite being a quick and efficient technology, it is more costly than other cutting methods. Furthermore, it can cause noise and generate water and abrasive debris, requiring proper management for worker safety and environmental compliance.
Sheet Metal Bending
Bending sheet metal involves shaping it into specific angles or shapes along a straight axis. This can be done manually or with machines like press brakes or folding machines. It’s a versatile technique that can create various shapes like L-shaped brackets, U-shaped channels, and Z-shaped profiles. Bending can also be combined with cutting, punching, and welding for complex assemblies.
Sheet Metal Punching
Sheet metal punching involves creating holes or shapes in a workpiece using a punch and die, offering versatility for various shapes like round and square holes, notches, and custom designs. It is precise and efficient for cutting metals, plastics, and composites in large-scale production. However, it can leave burrs and imperfections along edges, requiring additional finishing for a smooth surface, and may not be effective for very thick or hard materials.
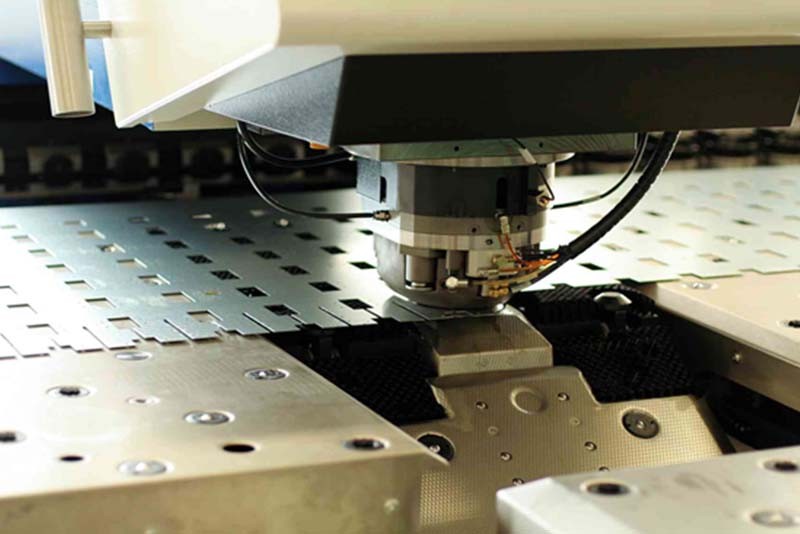
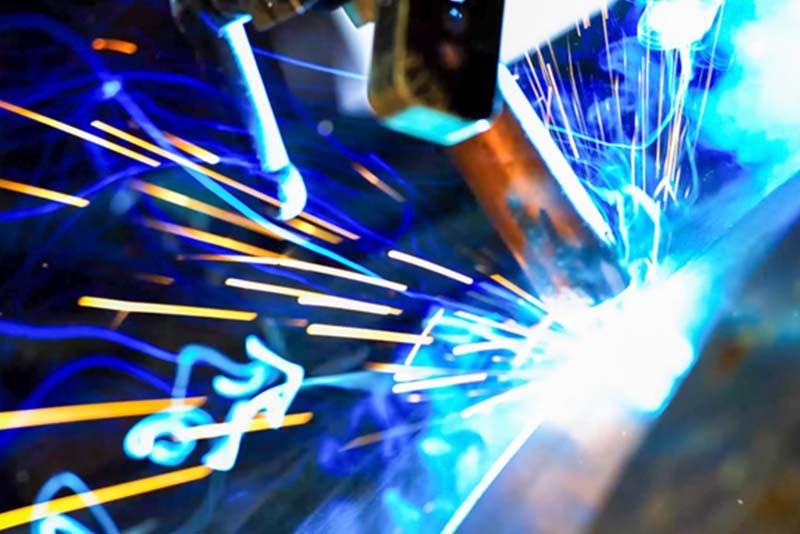
Sheet Metal Welding
Welding is a fascinating process that involves joining metal pieces together through the application of heat until they reach their melting point and unite. This technique possesses great adaptability, allowing for the fusion of various metal materials and differing levels of thickness, ranging from simple sheet metal joints to intricate assemblies with multiple components. One major benefit of welding is the creation of sturdy and enduring joints that exhibit remarkable resistance against high levels of stress. Furthermore, it offers the capability to produce practically invisible joints, allowing for a seamless and flawless finish. When it comes to large-scale production, welding proves to be a rapid and efficient method. Nevertheless, it is crucial to diligently monitor the heat input to prevent any deformations or distortions in the metal. There is also a possibility for weld spatter to form, which may require additional finishing processes for its elimination.
Material Selection for Sheet Metal Fabrication
Trust NOBLE to find the appropriate sheet metal fabrication material for your specific application and requirements, regardless of the nature of your project. Below, we have provided an overview of some commonly used materials for custom metal fabrication.
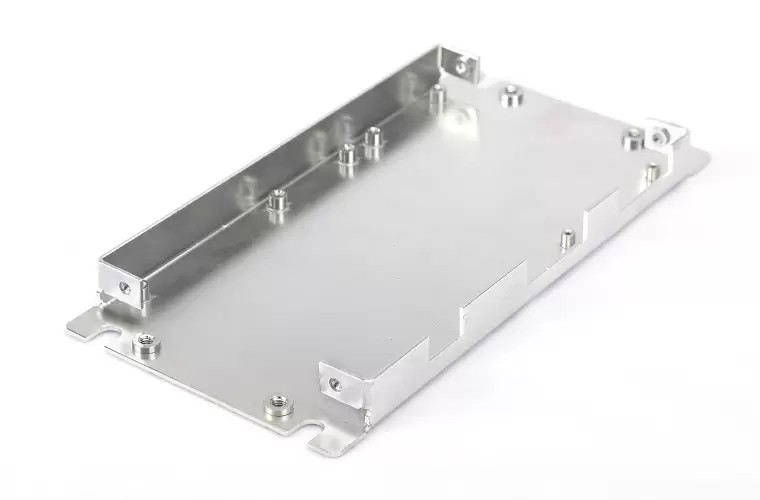
Aluminum
Aluminum is a highly favored material in the business industry for creating sheet metal because of its versatility, exceptional thermal conductivity, and low resistance. When compared to steel, aluminum not only offers cost-effectiveness but also enables faster production. Moreover, aluminum produces minimal waste and is easily recyclable, making it an environmentally friendly option for manufacturers.
Copper
Copper is often used in sheet metal fabrication in different industries because of its great malleability and ductility. Additionally, its excellent heat conduction and electrical conductivity properties make it a top choice for this process.
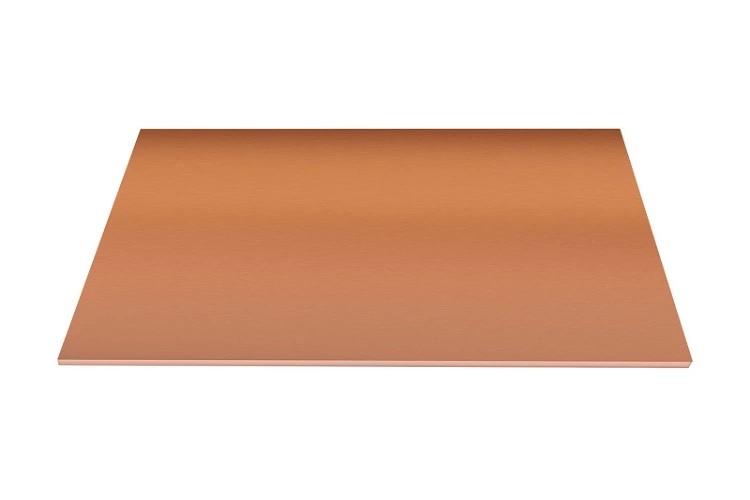
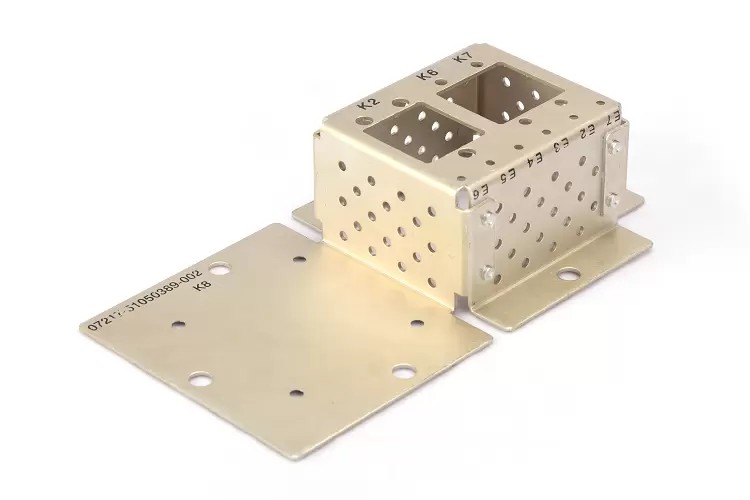
Brass
Brass is known for its many positive qualities that make it suitable for a wide range of applications. It has low friction, excellent electrical conductivity, and a unique golden color.
Steel
Steel has many benefits for industrial use, including being strong, long-lasting, able to withstand high heat, and resistant to rust. Steel sheet metal is perfect for creating detailed designs and precise components. Additionally, steel is affordable and can be polished to a high standard.
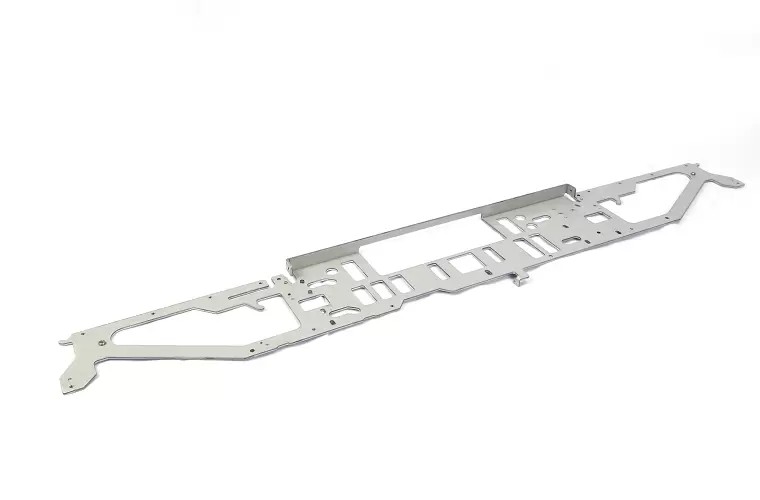
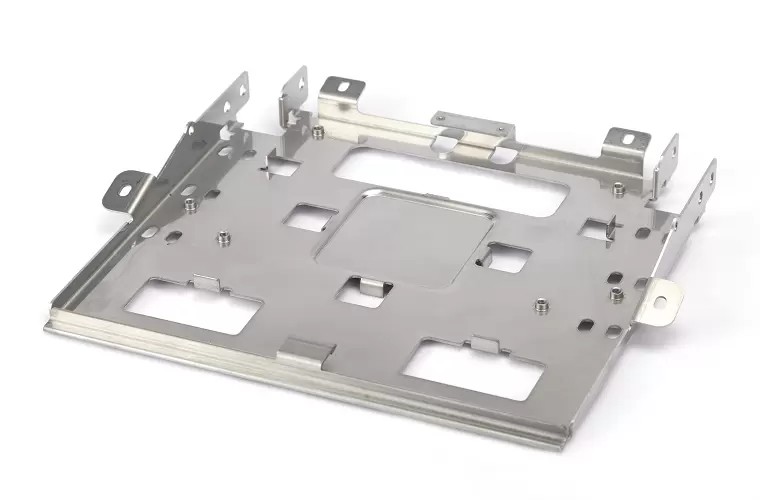
Stainless Steel
Stainless steel, a form of steel with a minimum of 10% chromium content by weight, finds extensive use in different sectors like construction, automotive, and aerospace owing to its exceptional material characteristics. Its adaptability makes it the favored choice for a multitude of applications in these industries.
Major Types of Sheet Metal
Hot Rolled Steel
The production of hot-rolled steel involves a method known as hot-rolling, where the steel is heated beyond its recrystallization temperature and rolled into various shapes. This steel type is recognized for its flexibility, strength, and cost-effectiveness. Widely applied in construction, manufacturing, and automotive fields for structural parts, pipes, and general uses, hot-rolled steel offers great weldability and formability, making it a versatile option for different applications that need sturdy and easily workable steel.
Pre-Plated Steel
The process of pre-coating steel entails applying a protective layer to different steel types before they are molded into their ultimate shape. This layer, usually composed of zinc or other metals, provides outstanding resistance to corrosion and extends the steel’s longevity. Pre-coated steel finds extensive application in sectors such as automotive, construction, and appliances, where preventing rust and corrosion is of paramount importance. The primary advantage of pre-coated steel lies in its immediate usability, thanks to the pre-installed protective layer, which reduces the necessity for additional surface treatments and enhances the durability of the final product.
Carbon steel
Known for its strength, durability, and cost-effectiveness, carbon steel is a widely utilized form of steel that consists predominantly of iron and carbon. Its versatility enables it to be easily shaped into various forms, making it a popular choice in diverse industries such as construction, automotive, machinery, and infrastructure. Through the use of heat treatment and alloying, its mechanical properties can be further enhanced. The exceptional tensile strength and capacity to endure substantial loads make carbon steel a dependable material in numerous industrial and commercial environments.
Galvanised steel
Galvanized steel is a type of steel that has been coated with zinc to protect it from rust. By immersing the steel in molten zinc, a strong and rust-resistant layer is formed. This type of steel is commonly used in construction, automotive, and manufacturing industries where preventing corrosion is essential. Its durability, strength, and affordability make it perfect for applications like roofing, fencing, structural components, and outdoor equipment. Galvanized steel presents a dependable and economical option for endeavors necessitating strong corrosion resistance.
Stainless steel
There are multiple stainless steel choices available for you to explore. Among them is stainless austenitic steel, which is a non-magnetic metal with high levels of nickel and chrome. These metals are often utilized due to their ease of shaping and resistance to corrosion. In contrast, ferritic stainless steel is magnetic and is suitable for applications that do not require structural or aesthetic purposes. Martensitic stainless steel is well-known for its ability to produce durable and corrosion-resistant items.
Aluminum
Aluminum is a versatile metal that combines strength with lightness, making it perfect for a wide array of uses. It also showcases exceptional resistance to corrosion. Utilized in industries such as packaging, construction, aerospace, and automotive, aluminum is widely appreciated for its durability, conductivity, and recyclability. It is featured in numerous products, from aircraft components to beverage containers.
Benefits of Sheet Metal Fabrication
Sheet metal fabrication provides a variety of advantages, making it a popular choice for many different applications. These benefits include simple brackets and enclosures, as well as complex structures and machinery.
Accuracy: Sheet metal fabrication provides a variety of advantages, making it a popular choice for many different applications. These benefits include simple brackets and enclosures, as well as complex structures and machinery.
Lightweight:Sheet metal is well-known for its lightweight properties, making it an ideal choice for situations where weight is crucial, especially in the aerospace and automotive industries.
Aesthetics:To achieve a polished and professional look for sheet metal, there are various techniques at your disposal. These methods include painting, polishing, and powder coating, each offering unique ways to enhance its appearance.
High-temperature resistance:Sheet metal is capable of withstanding high temperatures without compromising its structure or shape, making it suitable for use in environments such as furnaces and ovens where temperatures are elevated.
Easy to work with:Sheet metal is a versatile material that can be easily cut, shaped, and fused using welding techniques.This characteristic greatly facilitates its handling and assembly process.
Low maintenance:Sheet metal structures are recognized for their minimal upkeep needs, which makes them a very cost-effective option in the long run.
Applications of Sheet Metal Fabrication
Sheet metal fabrication is widely used in many industries for different reasons like giving structural support, improving visual attractiveness, and creating crucial parts for various products. Here are some notable instances of its broad applications.
Automotive parts Sheet Metal Fabrication
Sheet metal fabrication plays a crucial role in the automotive industry, being used to create car bodywork, structural parts, engine components, brackets, exhaust systems, and a variety of interior and exterior elements.
Aerospace parts Sheet Metal Fabrication
Sheet metal fabrication is essential in the aerospace industry because it produces lightweight, strong, and precise parts that greatly improve the performance, safety, and efficiency of an aircraft. These parts consist of wings, fuselages, frames, brackets, engine enclosures, and control surfaces.
Medical Equipment Sheet Metal Fabrication
Sheet metal fabrication is an essential process that greatly improves the strength, personalization, and performance of medical devices and equipment. By utilizing this technique, a wide range of components like cabinets, carts, trays, casings for medical instruments, hospital beds, and diagnostic equipment can be manufactured. These components play a vital role in enhancing the overall efficiency and effectiveness of healthcare facilities.
Energy and Power Generation Sheet Metal Fabrication
Sheet metal fabrication is vital in the energy sector as it creates important components for power plants like turbine casings, heat exchangers, pipes, and structural supports.
Industrial Machinery Sheet Metal Fabrication
Sheet metal fabrication presents a wide array of possibilities and advantages. It offers long-lasting and economical solutions for various industrial applications, such as machinery, structures, and operations. Its capabilities range from crafting custom-made components to improving the overall efficiency of manufacturing processes. Some common examples of fabricated sheet metal products include frames, enclosures, panels, shields, supports, and conveyor systems.
Electronics and Telecommunications Sheet Metal Fabrication
Sheet metal fabrication plays a crucial role in manufacturing electronic enclosures, racks, cabinets, chassis, brackets, and panels. These components are specifically designed to house electronic devices, servers, networking equipment, and telecommunications infrastructure.
Why choose MXY Custom Sheet Metal Fabrication?
MXY is a standout performer in the field of high-quality sheet metal fabrication services. We serve a wide array of sectors such as automotive, aerospace, robotics, medical, and more. Our team is made up of experienced professionals who are dedicated to delivering outstanding results, regardless of the complexity of the client’s project requirements. Equipped with cutting-edge technology and tools, we carry out every project with precision and accuracy. Whether you need a single prototype or large-scale production, our company provides a full range of sheet metal fabrication services at competitive prices. Our commitment is to deliver the best results within the specified timeframe and budget.
Quality and Accuracy Assurance
Demonstrating our commitment to quality, we have achieved ISO 9001:2015 and ISO 13485:2016 certifications. Through investments in cutting-edge machinery and technology, we provide excellent custom sheet metal fabrication services. Equipped with advanced tools and equipment, our facility enables us to conduct intricate fabrication processes with accuracy and efficiency. By staying updated on industry advancements, we deliver high-quality products, optimize production timelines, and reduce errors. Trust us to deliver sheet metal parts of exceptional quality and precision.
Customization and Flexibility
Our sheet metal processing services are renowned for their exceptional level of customization and adaptability. We recognize that each project is one-of-a-kind, often requiring distinct designs, measurements, or materials. To cater to the unique requirements of every customer, our team consistently collaborates with them through consultations. We place great emphasis on customization and assure that the end product perfectly matches the customer’s specifications, from the initial idea to the final result.The MXY engineers offer round-the-clock online engineering customer support for any custom sheet metal engineering and manufacturing concerns you may have. We provide personalized suggestions to help you save money in the initial phases of designing.
Customer Satisfaction
When it comes to custom sheet metal production, MXY places immense importance on quality control. We meticulously follow stringent quality standards and subject each stage of the manufacturing process to thorough inspection procedures. This meticulous attention to detail ensures that the end product is flawless and meets the highest quality criteria. Our ultimate priority is customer satisfaction, and we go the extra mile by providing dependable, long-lasting, and visually appealing sheet metal fabrication solutions. Our unwavering commitment to quality control and meeting client expectations sets us apart as a reliable option for custom sheet metal fabrication.
Sheet Metal Fabrication FAQs
1. What is considered fabrication?
Manufacturing involves creating items by combining standardized components with various techniques. For instance, steel fabrication includes crafting metal structures through methods like cutting, bending, and assembling.
2. What is fabrication material?
Fabrication materials play a crucial role in the construction or assembly of a product or component. These materials are the raw materials or substances used in the fabrication process. The choice of materials depends on the specific fabrication process and the desired end product, leading to the use of a diverse range of materials. Commonly used materials include aluminum, copper, stainless steel, brass, and steel.
3. What is the difference between sheet metal and forging?
Sheet metal fabrication is a versatile method employed to mold thin metal sheets, providing benefits like adaptability, precision, and lightweight parts. On the other hand, forging is a heat-dependent process that creates robust and durable metal components ideal for demanding tasks, although it has restrictions when it comes to intricate shapes.
4. What is sheet metal mainly used for?
Sheet metal is a valuable material due to its flexibility, durability, and cost-effectiveness. It is utilized across various industries such as automotive, construction, aerospace, and electronics to manufacture structural elements, enclosures, and cabinets.In essence, sheet metal serves as a fundamental building material across multiple sectors.
5. What are the three 3 types of metal fabrication?
Metal fabrication encompasses a range of techniques, which encompass cutting, forming, and welding. These techniques can be further divided into subcategories, such as laser cutting and plasma cutting for cutting, bending and stretching for forming, and MIG and TIG welding for welding.
6. What is basic metal fabrication?
Metal fabrication is the process of putting together, cutting, and shaping metal to create different structures. Using a metal fabrication tool to make holes, louvers, or unique shapes in metal is a standard procedure.Additionally, the process of removing material from metal using rotary cutters is referred to as milling.
7. How are sheet metal parts made?
In the realm of metal manufacturing, there are several conventional processes such as forming, casting, molding, joining, and machining. When it comes to sheet metal forming, force is applied to reshape the metal into the desired shape, leaving no excess material behind.
8. What are sheet metal components?
A variety of materials are commonly used for a range of applications. Sheets crafted from popular technical metals such as carbon steel, stainless steel, copper, and aluminum are extensively employed. The material chosen depends on the specific requirements and specifications of the product being utilized.