First of all, before diving into the details, you need to understand what precision turning is. Precision turning is the removal of excess material from the workpiece to reduce its size and convert its size to the desired size so that it can fit where we need it. So basically, it involves cutting additional material to get the desired shape of the material.
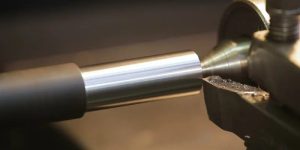
Precision machining before the invention of CNC
In the past, prior to the development of CNC machine tools, workers were able to achieve precision in taper, turning, cutting, drilling, and other processes using traditional tools like blades, saws, and hammers. However, this method required more labor and time. With advancements in technology, precision has significantly improved. Nowadays, precision machining of various materials such as wood, metal, and plastic can be easily accomplished.
Advantages of precision CNC machining
CNC technology is a groundbreaking advancement in precision machining as it enables the execution of multiple high-precision machining tasks simultaneously, particularly precision turning. This is made possible by a compact digital computer that is programmed based on specific requirements, allowing the machine to carry out all processes as instructed by the computer program. To ensure smooth and safe operation, skilled technicians and operators are essential in running these machines. CNC aluminum machining has become a common occurrence in numerous factories, playing a significant role in our daily lives. When compared to conventional processing methods, CNC machine tools offer numerous advantages, a few of which are outlined below:
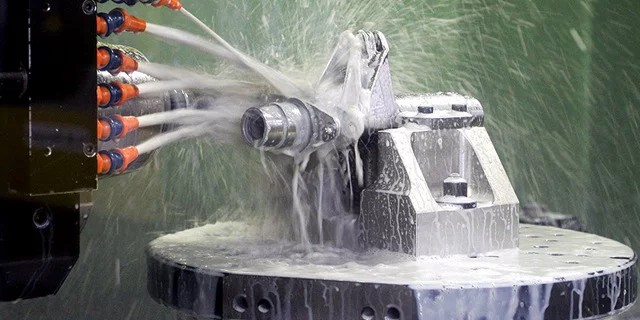
- Enhanced precision and accuracy – create parts with exceptional precision and accuracy in a shorter amount of time.
- Efficiency – This method is highly efficient when compared to conventional machining techniques.
- Economical benefits – Reduced foundry expenses are a result of decreased labor and resource requirements.
- Safety – With minimal interaction required with the machine, this process is significantly safer than traditional machining methods. In CNC machine tools, simply input the program into the computer and let the machine handle the rest.
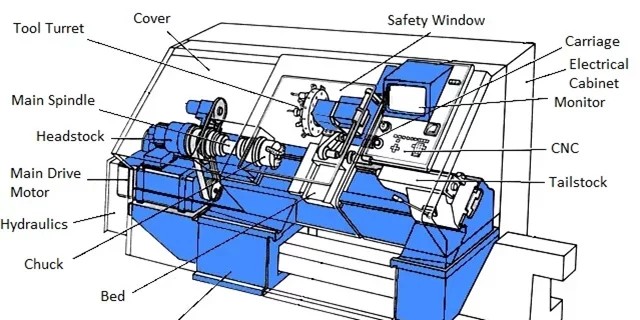
Table of Contents
CNC high precision turning
CNC turning is the method used to produce precise turning parts using lathes. It is a sophisticated engineering process that is utilized to fabricate intricate components for various applications. While the fundamental technique resembles that of conventional lathes, CNC lathes are computer-controlled, ensuring precise control over motor speed, cutting tool speed, and eliminating the possibility of errors.
Advanced CNC lathes and CNC components enable the production of intricate details with minimal tolerances for precise work. The lathe operates under the complete control of a computer program that monitors each machining step in the project.
The difference between CNC turning and CNC milling
CNC milling and CNC turning enable individuals to produce custom machined parts with intricate details and achieve precise results.
In the realm of CNC milling, the operator is required to configure and input a program into the computer system, subsequently initiating its execution. The spindle is then set in motion along its axis, meticulously slicing through the surplus material via precision turning to fabricate turning components. By harnessing computer programming, one can achieve accurate and incisive cuts.
CNC turning involves the use of computer-controlled machinery to create a unique end product. A single-point cutting tool is utilized in this process, positioned parallel to the workpiece to eliminate chips. The tool spins at a variable speed, while the cutting action moves sideways to produce a cylindrical groove with precise dimensions. Unlike other methods, CNC turning does not craft round or hollow shapes from bulkier materials. This automated technique adjusts its speed for improved precision, eliminating the need for manual adjustments on the shaping equipment.
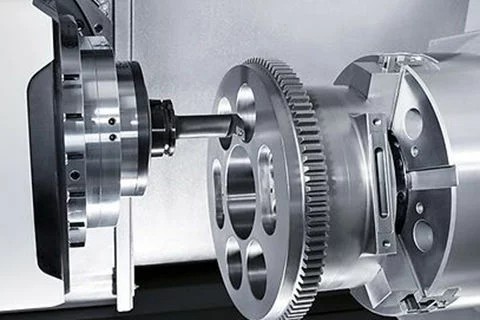
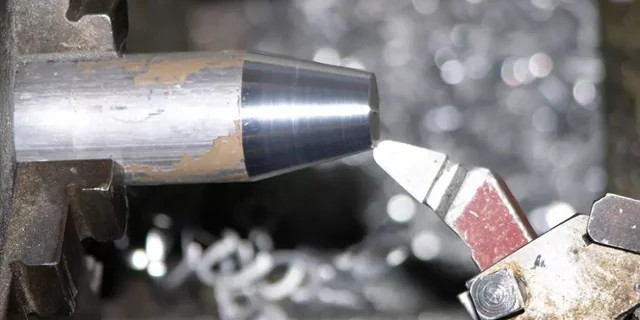
Which parts need high precision turning?
Undoubtedly, CNC turning and CNC milling are distinct processes that yield varying outcomes. The CNC center is most suitable for small batch production, particularly for prototypes exceeding 0.25D, whereas the turning center can be employed for prototypes above 0.25D. Each of these methods necessitates individual assessment based on the specific part being produced, which inevitably impacts the cost of the component. If you find yourself in a situation where you need to manufacture certain parts but are unsure whether to opt for CNC milling or CNC turning, seeking a second opinion is advisable.
There is a significant demand for high precision CNC turning parts or custom parts across various industries, such as automotive, biomedical, aviation, instrumentation, robotics, and more.